ERP for 3D Printing and Prototyping Services: Enhance Efficiently
Our specialized ERP solution is designed to revolutionize your 3D printing and prototyping services. Whether you’re managing a small operation or a large-scale production, our ERP system streamlines every aspect of your business. From order processing and inventory management to production scheduling and quality control, our ERP integrates seamlessly into your workflow, providing real-time insights and automation to enhance efficiency. With robust tools for cost management, customer relationship management (CRM), and detailed reporting, our ERP empowers you to meet tight deadlines, reduce errors, and maximize profitability. Tailored to the unique needs of the 3D printing industry, our ERP ensures you stay ahead of the competition.
Pain Points and ERP Solutions for 3D Printing and Prototyping Services
Inefficient Workflow Management
Pain Point:
Disorganized processes can lead to delays and errors in production.
Solution:
Our custom ERP system streamlines workflow by automating tasks and providing real-time updates, ensuring smoother and more efficient operations.
Complex Inventory Tracking
Pain Point:
Managing inventory manually is time-consuming and prone to inaccuracies.
Solution:
The ERP offers automated inventory tracking and management, reducing manual errors and optimizing stock levels for better resource allocation.
Difficulty in Production Scheduling
Pain Point:
Scheduling conflicts and uncoordinated tasks can disrupt production timelines.
Solution:
Our ERP includes advanced scheduling tools that align production schedules with order requirements, minimizing delays and maximizing productivity.
Ineffective Cost Management
Pain Point:
High production costs and budgeting challenges can impact profitability.
Solution:
The ERP provides comprehensive cost management features, including expense tracking and budgeting tools, helping you control costs and improve financial performance.
Poor Quality Control
Pain Point:
Ensuring consistent quality can be challenging without proper oversight.
Solution:
Integrated quality control modules in our ERP allow for systematic checks and documentation, ensuring that products meet quality standards.
Lack of Real-Time Data
Pain Point:
Limited access to real-time data hinders decision-making and responsiveness.
Solution:
Our ERP delivers real-time analytics and reporting, giving you actionable insights to make informed decisions quickly and efficiently.
Customer Relationship Management Challenges
Pain Point:
Maintaining customer relationships and managing interactions can be cumbersome.
Solution:
The ERP features a CRM module to manage customer interactions, track orders, and enhance communication, leading to improved customer satisfaction.
See How My Company Can Massively Automate Your Company Departments
Custom CRM Development – For Organizations to manage its Customer Interactions in addition to Sales, Marketing, Billing, Products, Services, Contacts, Customer Support, among other things.
Custom ERP Development – For Manufacturers to handle BOM, Quotation, Order, RFQ, PO, SOA, Manufacturing, Trading, Inventory, Quality Control, Logistics, Shipments, and so on.
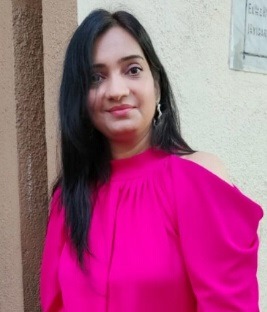
Difficulties in Tracking Project Progress
Pain Point:
Tracking project status manually can lead to miscommunication and missed deadlines.
Solution:
With project management tools integrated into the ERP, you can monitor project progress, manage tasks, and ensure timely completion of projects.
Features
Order Management
Streamlines the entire order lifecycle from receipt to fulfillment.
Includes tracking, prioritization, and real-time status updates.
Inventory Management
Automated tracking of raw materials and finished products.
Real-time updates on stock levels, reordering, and material usage.
Production Scheduling
Advanced tools for scheduling and managing production runs.
Coordination of resources and machinery to optimize production efficiency.
Cost Management
Comprehensive tracking of production costs, including materials, labor, and overhead.
Budgeting tools to manage and control expenses effectively.
Quality Control
Integrated quality checks and inspections throughout the production process.
Documentation and reporting features to ensure compliance with quality standards.
Project Management
Tools for planning, tracking, and managing projects.
Task assignment, progress tracking, and milestone management.
Customer Relationship Management (CRM)
Centralized database for managing customer interactions and information.
Features for tracking sales, customer inquiries, and service requests.
Real-Time Reporting and Analytics
Dashboards and reports for real-time insights into operations, sales, and performance metrics.
Customizable reports to analyze trends and make data-driven decisions.
Document Management
Storage and management of documents related to projects, orders, and quality control.
Secure access and version control for critical documents.
Supply Chain Management
Integration with suppliers and logistics for efficient procurement and delivery.
Tracking of supplier performance and material sourcing.
Maintenance Management
Tools for scheduling and tracking maintenance of 3D printers and other equipment.
Preventive maintenance alerts to minimize downtime.
Resource Management
Allocation and tracking of human resources, machinery, and other assets.
Optimization of resource utilization to enhance productivity.
Integration Capabilities
Seamless integration with other software systems, such as CAD tools and financial software.
API support for connecting with third-party applications.
User Access Control
Role-based access control to ensure security and data privacy.
Customizable permissions for different user roles within the organization.
Customer Portal
Self-service portal for customers to place orders, track status, and manage their accounts.
Enhances customer experience and reduces manual administrative tasks.
These features ensure that an ERP system can comprehensively manage and optimize all aspects of 3D printing and prototyping services, from order processing to production and customer management.