ERP for Cleaning and Hygiene Products: Automate Manufacturing
In today’s rapidly evolving market, the cleaning and hygiene products industry faces numerous challenges. Manufacturers of cleaning agents, disinfectants, laundry detergents, and other household cleaning products must overcome various pain points to remain competitive. These pain points include production planning complexities, inventory control issues, quality assurance concerns, supply chain management difficulties, regulatory compliance tracking, order management complexities, and distribution inefficiencies. However, with the implementation of a customized ERP for cleaning and hygiene products, these pain points can be effectively addressed, streamlining operations and improving overall business performance.
Optimizing Production Planning and Timely Delivery through Data Utilization
Inventory Control Issues:
Maintaining optimal inventory levels is crucial for cleaning and hygiene product manufacturers. Overstocking can tie up working capital, while understocking can lead to missed sales opportunities and dissatisfied customers. A customized ERP solution can enable manufacturers to track inventory levels, automate reorder points, and streamline inventory management. By having accurate real-time information on stock levels, manufacturers can avoid stockouts, reduce carrying costs, and make informed procurement decisions.
Quality Assurance Concerns:
Ensuring product quality and safety is paramount in the cleaning and hygiene products industry. A customized ERP system can integrate quality control processes into the manufacturing workflow. By implementing quality checkpoints at various stages of production, manufacturers can monitor and measure product quality parameters. This proactive approach allows for early detection and resolution of quality issues, reducing the risk of product recalls and customer complaints.
Production Planning Complexities:
One of the significant challenges in the cleaning and hygiene products industry is optimizing production planning. Manufacturers need to balance the demand for a diverse range of products with efficient resource allocation. A customized ERP system can provide real-time visibility into production capacities, inventory levels, and customer demand.
Supply Chain Management Difficulties:
Managing a complex network of suppliers, distributors, and logistics partners can be challenging for cleaning and hygiene product manufacturers. A customized ERP solution can facilitate seamless supply chain management by automating and optimizing key processes. With real-time visibility into supplier performance, manufacturers can make informed decisions about supplier selection, negotiate better terms, and improve overall supply chain efficiency.
Regulatory Compliance Tracking:
The cleaning and hygiene products industry is subject to stringent regulations and compliance requirements. Staying up-to-date with regulatory changes and ensuring compliance across the product portfolio can be overwhelming. A customized ERP system can centralize regulatory information, track compliance updates, and automate documentation processes. By integrating compliance checks into the system, manufacturers can streamline regulatory audits, minimize compliance risks, and ensure product safety and legality.
Order Management Complexities:
Managing orders efficiently is crucial for meeting customer expectations and maintaining satisfaction. A customized ERP solution can streamline the order management process, from order capture to fulfillment. By integrating the ERP system with customer relationship management (CRM) tools, manufacturers can automate order processing, track order status in real-time, and provide accurate delivery estimates. This reduces order processing time, minimizes errors, and enhances customer satisfaction.
Distribution Inefficiencies:
The distribution of cleaning and hygiene products involves coordinating multiple channels, warehouses, and transportation logistics. Manual processes and disparate systems can lead to delays, inaccuracies, and higher costs. A customized ERP solution can optimize distribution by providing end-to-end visibility into the supply chain. Manufacturers can track inventory movement, manage warehouse operations, and optimize transportation routes. This results in faster order fulfillment, reduced shipping costs, and improved customer service.
See How My Company Can Massively Automate Your Company Departments
Custom CRM Development – For Organizations to manage its Customer Interactions in addition to Sales, Marketing, Billing, Products, Services, Contacts, Customer Support, among other things.
Custom ERP Development – For Manufacturers to handle BOM, Quotation, Order, RFQ, PO, SOA, Manufacturing, Trading, Inventory, Quality Control, Logistics, Shipments, and so on.
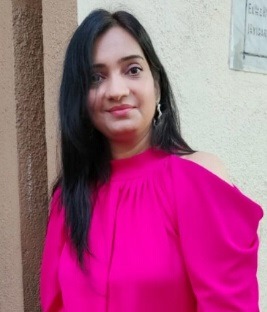
Conclusion
The cleaning and hygiene products industry faces several pain points that can impede business growth and customer satisfaction. However, by implementing a customized ERP for Cleaning and Hygiene Products, manufacturers can overcome these challenges and streamline their operations. From production planning to order management and distribution, a tailored ERP system offers real-time visibility, automation, and optimization capabilities. By harnessing the power of ERP, cleaning and hygiene product manufacturers can enhance efficiency, ensure product quality and safety, comply with regulations, and meet market demands. Ultimately, a customized ERP solution empowers businesses to deliver high-quality cleaning and hygiene products, gain a competitive edge, and drive success in a dynamic industry.
Use Case: Optimizing Production and Supply Chain Management for a Cleaning and Hygiene Products Manufacturer
ABC Cleaning Solutions is a leading manufacturer of cleaning agents, disinfectants, and household cleaning products. With a diverse product portfolio and a strong commitment to quality, ABC Cleaning Solutions has gained a significant market share. However, the company is facing challenges in managing production planning, inventory control, and supply chain management. To overcome these pain points, ABC Cleaning Solutions decides to implement a customized ERP solution.
Pain Points
Production Planning Challenges:
Difficulty in balancing production capacities with diverse product demands.
Inefficient resource allocation leading to bottlenecks and delays.
Lack of real-time visibility into production schedules and raw material availability.
Inventory Control Issues:
Carrying excessive inventory, tying up working capital.
Frequent stockouts resulting in missed sales opportunities.
Inaccurate inventory data leading to procurement inefficiencies.
Supply Chain Management Difficulties:
Manual processes and disparate systems causing coordination challenges.
Lack of visibility into supplier performance and delivery timelines.
Inefficient logistics leading to increased costs and delayed shipments.
Implementing a Customized ERP System
ABC Cleaning Solutions recognizes that a tailored ERP solution can address their pain points and streamline their operations. They partner with a leading ERP provider to implement a customized solution that caters specifically to their needs.
Benefits
Streamlined Production Planning:
The ERP system provides real-time visibility into production capacities, helping ABC Cleaning Solutions optimize resource allocation.
Accurate demand forecasting and inventory data enable proactive production planning, minimizing bottlenecks and delays.
Automated scheduling and notifications ensure timely production and delivery, enhancing customer satisfaction.
Efficient Inventory Control:
The ERP system integrates inventory management modules, providing real-time data on stock levels, movement, and expiration dates.
Automated reorder points and alerts prevent stockouts and minimize overstocking.
Accurate inventory data enables informed procurement decisions, reducing carrying costs and improving cash flow.
Enhanced Supply Chain Management:
The ERP system integrates suppliers’ data and performance metrics, enabling ABC Cleaning Solutions to evaluate and select the most reliable suppliers.
Real-time visibility into supplier inventory and delivery schedules enables proactive management of the supply chain.
Streamlined logistics management, including warehouse operations and transportation optimization, reduces costs and ensures on-time deliveries.
Regulatory Compliance and Quality Assurance:
The ERP system centralizes regulatory information and automates compliance checks.
Quality control checkpoints are integrated into the manufacturing process, ensuring adherence to quality standards and reducing the risk of product recalls.
Automated documentation processes facilitate regulatory audits, saving time and ensuring compliance with industry regulations.
Efficient Order Management and Distribution:
The ERP system integrates order management and customer relationship management (CRM) functionalities.
Order processing is streamlined, from order capture to fulfillment, reducing errors and processing time.
Real-time order tracking and accurate delivery estimates improve customer satisfaction and loyalty.
Optimized distribution processes, including warehouse management and transportation planning, result in faster order fulfillment and reduced shipping costs.
Conclusion
By implementing a customized ERP system, ABC Cleaning Solutions successfully overcomes their pain points in production planning, inventory control, and supply chain management. The tailored ERP solution enables them to optimize resource allocation, minimize stockouts, streamline logistics, ensure regulatory compliance, and improve customer satisfaction. ABC Cleaning Solutions experiences enhanced operational efficiency, cost reduction, and increased competitiveness in the dynamic cleaning and hygiene products market.