ERP for Electric Pasta Maker Manufacturers: Complete Automation
The electric pasta maker manufacturing industry is rapidly evolving, with increased demand for homemade and fresh pasta. However, along with this growth comes various challenges that can hinder the efficiency and profitability of businesses in this sector. In order to overcome these pain points, implementing a customized Enterprise Resource Planning (ERP) solution specifically tailored for electric pasta maker manufacturers can be the key to success. This article will explore the pain points faced by such businesses and explain how a customized ERP system can effectively resolve these challenges.
Pain Points
Inefficient Production Scheduling:
One of the major pain points for electric pasta maker manufacturers is the lack of efficient production scheduling. Without proper coordination between production lines, delays, bottlenecks, and inefficiencies can occur, leading to increased costs and missed delivery deadlines. A customized ERP system can address this issue by providing a centralized platform to manage and optimize production schedules. It enables real-time visibility into production processes, allowing manufacturers to allocate resources effectively, streamline workflows, and reduce idle time.
Inventory Control and Order Processing Challenges:
Maintaining optimal inventory levels and managing the order processing cycle can be complex and time-consuming for electric pasta maker manufacturers. Manual inventory tracking often leads to stockouts, excess inventory, and difficulties in fulfilling customer orders promptly. A customized ERP solution can automate these processes, providing real-time inventory management capabilities. It enables accurate demand forecasting, tracks inventory levels, and automates the order processing cycle from procurement to delivery. This ensures that the right amount of raw materials and finished products are available at the right time, minimizing waste and improving customer satisfaction.
Supplier Management and Procurement Complexity:
Electric pasta maker manufacturers rely on a network of suppliers for various components and raw materials. Coordinating with multiple suppliers, ensuring timely deliveries, and maintaining quality standards can be a daunting task. A customized ERP system simplifies supplier management by providing a centralized database for supplier information, contracts, and performance evaluations. It streamlines procurement processes, automates purchase orders, and enables better collaboration with suppliers, resulting in improved supplier relationships, cost savings, and enhanced product quality.
Limited Sales Insights and Inefficient Analytics:
Understanding sales trends, customer preferences, and market demands is crucial for electric pasta maker manufacturers to make informed business decisions. However, without a robust analytics system, it becomes challenging to gather, analyze, and interpret data effectively. A customized ERP solution offers advanced analytics and reporting capabilities, allowing businesses to track sales trends, identify patterns, and gain actionable insights. This enables manufacturers to optimize inventory levels, adjust production volumes based on demand, and develop targeted marketing strategies to drive growth and increase profitability.
See How My Company Can Massively Automate Your Company Departments
Custom CRM Development – For Organizations to manage its Customer Interactions in addition to Sales, Marketing, Billing, Products, Services, Contacts, Customer Support, among other things.
Custom ERP Development – For Manufacturers to handle BOM, Quotation, Order, RFQ, PO, SOA, Manufacturing, Trading, Inventory, Quality Control, Logistics, Shipments, and so on.
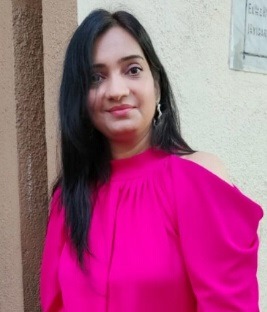
Conclusion
The electric pasta maker manufacturing industry is poised for growth, but businesses in this sector must overcome various pain points to thrive in a competitive market. A customized ERP system tailored specifically for electric pasta maker manufacturers provides a comprehensive solution to address these challenges. From streamlining production scheduling and inventory control to simplifying supplier management and leveraging analytics, an ERP system enhances operational efficiency, reduces costs, and enables businesses to deliver homemade and fresh pasta with utmost precision and customer satisfaction. By embracing the power of technology and automation, electric pasta maker manufacturers can position themselves for success in the dynamic market landscape.
Use Case: Optimizing Production Efficiency and Inventory Control with ERP for Electric Pasta Maker Manufacturing
Company Profile:
PastaMaster Inc. is a leading manufacturer of electric pasta makers, catering to both professional and home chefs. With a wide range of innovative pasta machines, the company has established a strong reputation for quality and reliability. As PastaMaster Inc. experiences rapid growth, it faces several pain points related to production scheduling, inventory control, and order processing. To overcome these challenges, the company decides to implement a customized Enterprise Resource Planning (ERP) solution.
Challenge
PastaMaster Inc. is struggling with inefficient production scheduling, leading to delays, idle time, and increased costs. The manual process of managing inventory and order processing is time-consuming and prone to errors, resulting in stockouts, excess inventory, and delayed customer deliveries. The company also faces challenges in supplier management, often experiencing difficulties in coordinating with multiple suppliers and ensuring timely deliveries. Moreover, PastaMaster Inc. lacks a comprehensive analytics system to gain insights into sales trends and customer preferences, hindering effective decision-making.
Implementing a Customized ERP System
Streamlined Production Scheduling:
PastaMaster Inc. integrates a customized ERP system that offers a centralized platform for managing and optimizing production schedules. The ERP system provides real-time visibility into production processes, allowing the company to allocate resources effectively, identify bottlenecks, and streamline workflows. By automating the scheduling process and providing accurate production forecasts, the ERP system minimizes idle time, reduces costs, and improves overall production efficiency.
Enhanced Inventory Control and Order Processing:
The customized ERP solution enables PastaMaster Inc. to gain control over inventory management and order processing. With real-time data on inventory levels, the company can accurately forecast demand and maintain optimal stock levels. The ERP system automates the entire order processing cycle, from procurement to delivery, eliminating manual errors and ensuring timely fulfillment of customer orders. By improving inventory control and order processing, PastaMaster Inc. reduces stockouts, minimizes excess inventory, and enhances customer satisfaction.
Simplified Supplier Management and Procurement:
The ERP system centralizes supplier information, contracts, and performance evaluations, simplifying supplier management for PastaMaster Inc. It streamlines procurement processes by automating purchase orders and providing real-time updates on supplier availability and delivery schedules. By optimizing supplier relationships and ensuring timely deliveries of quality materials, the ERP system helps the company maintain a reliable supply chain, reduce costs, and enhance product quality.
Empowered Analytics and Reporting:
PastaMaster Inc. utilizes the robust analytics and reporting capabilities of the ERP system. It gains valuable insights into sales trends and customer preferences. The ERP system collects and analyzes data from various sources. This enables the company to identify patterns, forecast demand, and make informed business decisions. With accurate sales insights, PastaMaster Inc. can optimize inventory levels. It can also adjust production volumes based on demand and develop targeted marketing strategies to drive growth and profitability.
Results
By implementing the customized ERP system, PastaMaster Inc. experiences significant improvements across its operations. Production scheduling becomes streamlined, reducing delays and idle time. Inventory control and order processing are optimized, leading to reduced stockouts, minimized excess inventory, and improved customer satisfaction. Supplier management and procurement processes are simplified, resulting in better collaboration with suppliers and enhanced product quality. The ERP system’s analytics capabilities provide valuable insights, enabling PastaMaster Inc. to make informed decisions and improve overall business performance.
Conclusion
By using an ERP, PastaMaster Inc. overcomes its pain points in production scheduling, inventory control, order processing and supplier management. The ERP solution empowers the company to optimize production efficiency, maintain optimal inventory levels, streamline order processing, and enhance supplier relationships. With robust analytics and reporting capabilities, PastaMaster Inc. gains valuable insights into sales trends and customer preferences. It enables data-driven decision-making and driving growth and profitability. The ERP system proves to be a transformative solution for PastaMaster Inc. It positioned the company as a leader in the electric pasta maker manufacturing industry.