Custom ERP for Hair Treatment and Mask Manufacturers
The hair treatment and mask manufacturing industry has experienced significant growth in recent years due to the increasing demand for deep conditioning and nourishing products for hair care. As manufacturers strive to meet consumer expectations, they encounter several challenges in managing their production processes, ingredient inventory, and formulation accuracy. To address these pain points, a customized Enterprise Resource Planning (ERP) system can prove to be a game-changer. This article explores the pain points faced by hair treatment and mask manufacturers and presents an innovative solution through a tailored ERP system.
Pain Points and ERP Solutions
Complex Production Processes and Lack of Visibility
Pain Point:
Manufacturing hair treatments and masks involve multiple intricate steps, from ingredient mixing to product packaging. Manufacturers often struggle to manage and streamline these complex processes efficiently. The lack of real-time visibility into each stage of production hampers decision-making and coordination among various departments, leading to delays, inefficiencies, and potential quality issues.
Solution: A Customized ERP for Seamless Production Management
A tailored ERP system can integrate and automate the entire production process, from formulation to packaging, providing real-time insights into each stage. This centralized platform allows manufacturers to monitor production progress, identify bottlenecks, and allocate resources effectively. With improved visibility, managers can make informed decisions, optimize workflows, and ensure timely deliveries of high-quality products.
Ingredient Inventory Management Challenges
Pain Point:
Hair treatment and mask manufacturers must maintain a vast inventory of ingredients with varying shelf lives and storage requirements. Manual inventory management can lead to inaccuracies, stockouts, or overstocking, resulting in increased costs and production delays.
Solution: ERP-Driven Inventory Optimization
A customized ERP system can track ingredient levels in real-time, ensuring optimal inventory levels based on historical data and demand forecasts. Automated notifications for low stock levels enable timely reordering, preventing production interruptions. Furthermore, the ERP system can help with batch tracking, ensuring proper usage of ingredients based on first-in-first-out (FIFO) principles, thus reducing wastage and improving cost-efficiency.
Formulation Accuracy and Compliance
Pain Point:
Accurate formulation of hair treatments and masks is vital to deliver consistent and effective products. Manual formulation processes can lead to errors and deviations, compromising product quality and compliance with regulatory standards.
Solution: Enhanced Formulation Control through ERP
A customized ERP system can store precise formulations, ensuring accurate ingredient measurements and adherence to established standards. The ERP can also maintain detailed records of each product batch, facilitating traceability and regulatory compliance. By automating formulation processes, manufacturers can eliminate human errors, achieve consistent product quality, and confidently meet industry regulations.
Inefficient Packaging and Labeling
Pain Point:
Packaging and labeling play a crucial role in product presentation and brand identity. Inefficient manual packaging processes can lead to packaging errors, mislabeled products, and delays in shipment.
Solution: Streamlined Packaging with ERP Integration
A customized ERP system can automate packaging instructions and streamline labeling processes. By integrating the ERP with the packaging machinery, manufacturers can ensure accurate and standardized packaging, reducing the risk of errors and enhancing overall efficiency. Additionally, the ERP system can manage batch-specific labeling requirements, allowing for swift compliance with regional regulations.
See How My Company Can Massively Automate Your Company Departments
Custom CRM Development – For Organizations to manage its Customer Interactions in addition to Sales, Marketing, Billing, Products, Services, Contacts, Customer Support, among other things.
Custom ERP Development – For Manufacturers to handle BOM, Quotation, Order, RFQ, PO, SOA, Manufacturing, Trading, Inventory, Quality Control, Logistics, Shipments, and so on.
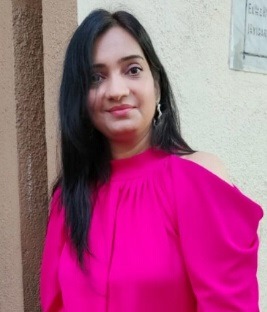
Ineffective Resource Management
Pain Point:
Optimizing resource allocation, including manpower and machinery, is essential for maintaining a competitive edge. Manual resource management can be challenging, leading to underutilization or overburdening of resources.
Solution: Resource Optimization through ERP Insights
A tailored ERP system can analyze production data and provide valuable insights into resource utilization. By identifying patterns and inefficiencies, manufacturers can make informed decisions to optimize resource allocation, reduce downtime, and maximize productivity. ERP-driven resource planning enables better workforce scheduling, ensuring that skilled personnel are available when needed, thus improving overall operational efficiency.
Conclusion
The hair treatment and mask manufacturing business is poised for continued growth, driven by consumer demand for high-quality and effective hair care products. However, manufacturers face several pain points that hinder their ability to meet customer expectations and operate with optimal efficiency.
A customized ERP system presents an innovative solution to these challenges, streamlining production processes, optimizing ingredient inventory management, ensuring formulation accuracy, enhancing packaging and labeling efficiency, and optimizing resource allocation. By embracing ERP technology, hair treatment and mask manufacturers can position themselves for success, delivering top-notch products while staying ahead of the competition in this dynamic industry.
Use Case: Streamlining Hair Treatment and Mask Manufacturing with Customized ERP
Enhancing Efficiency and Quality for Hair Treatment and Mask Manufacturers with Custom ERP Implementation
“NaturalGlow,” a leading hair treatment and mask manufacturing company, has experienced steady growth in recent years due to its commitment to producing high-quality products that provide deep conditioning and nourishment to the hair. However, as the company expanded its product portfolio and customer base, it encountered several challenges in managing production processes, ingredient inventory, formulation accuracy, and packaging efficiency. To address these pain points and maintain its competitive edge, NaturalGlow decided to implement a customized Enterprise Resource Planning (ERP) system.
Objective
The primary objective of NaturalGlow is to enhance operational efficiency, ensure accurate formulation, optimize resource utilization, and improve product quality and packaging through the implementation of a tailored ERP solution.
Key Pain Points
- Complex Production Processes and Lack of Visibility
- Ingredient Inventory Management Challenges
- Formulation Accuracy and Compliance
- Inefficient Packaging and Labeling
- Ineffective Resource Management
Custom ERP Implementation
Streamlining Production Processes and Enhancing Visibility
NaturalGlow implements an ERP system that integrates all aspects of production, from raw material sourcing to finished product packaging. The ERP platform provides real-time visibility into each production stage, allowing managers to monitor progress, identify bottlenecks, and make data-driven decisions for optimized workflows. With the ability to track production metrics, the company can efficiently manage resources and ensure timely deliveries.
Efficient Ingredient Inventory Management
The ERP system enables NaturalGlow to maintain accurate and real-time records of ingredient inventory. Based on historical data and demand forecasts, the ERP system generates automatic notifications for reordering when ingredient levels reach predetermined thresholds. This eliminates the risk of stockouts and overstocking, reducing costs and ensuring continuous production.
Ensuring Formulation Accuracy and Compliance
NaturalGlow’s customized ERP stores precise formulations for each product. When initiating production, the system guides operators through the accurate measurement of ingredients, minimizing human errors and deviations. By adhering to standardized formulations, the company can ensure consistent product quality. Moreover, the ERP system maintains detailed batch records, streamlining traceability and aiding in regulatory compliance.
Streamlined Packaging and Labeling
The ERP integration with packaging machinery allows NaturalGlow to automate packaging instructions and labeling processes. The ERP system ensures that the correct packaging materials are used, reducing errors and mislabeled products. Additionally, the ERP software manages batch-specific labeling requirements, streamlining compliance with various regional regulations.
Optimized Resource Utilization
With the ERP system analyzing production data, NaturalGlow gains insights into resource utilization patterns. The company can identify underutilized or overburdened resources, enabling informed resource allocation decisions. By optimizing workforce scheduling and machine usage, NaturalGlow reduces downtime and maximizes overall operational efficiency.
Benefits
- Enhanced production efficiency and reduced lead times.
- Improved product quality and consistency.
- Reduced ingredient wastage and optimized inventory levels.
- Increased compliance with regulatory standards.
- Streamlined packaging processes, minimizing errors.
- Efficient resource management, lowering operational costs.
Conclusion
By implementing a customized ERP system, NaturalGlow successfully addresses its pain points in hair treatment and mask manufacturing. The ERP solution streamlines production processes, improves ingredient inventory management, ensures formulation accuracy, enhances packaging efficiency, and optimizes resource utilization. With increased efficiency and quality assurance, NaturalGlow remains a competitive force in the hair care industry, meeting customer demands and achieving sustained growth.