Hair Color Manufacturing ERP
The hair color manufacturing industry has experienced significant growth in recent years as consumers seek creative and expressive ways to experiment with their appearance. Manufacturers producing hair sprays, hair chalks, and wash-out hair dyes face unique challenges in managing their production processes efficiently while meeting customer demands for a wide range of color options. To tackle these pain points, a customized Hair Color Manufacturing ERP system tailored to the specific needs of the hair color manufacturing business can offer transformative solutions.
Pain Points and Solutions
Pain Point – Complex Inventory Management:
One of the primary pain points for hair color manufacturers is handling a diverse inventory of raw materials, color pigments, packaging, and finished products. Traditional inventory management methods often lead to inefficiencies, resulting in stockouts, overstocking, and increased production costs.
Customized ERP Solution:
A tailor-made ERP system can implement real-time inventory tracking, ensuring that manufacturers have an accurate view of their material availability at all times. Automated reorder points and stock alerts can be integrated, optimizing the procurement process and reducing the chances of stockouts. Additionally, the system can enable the optimization of batch sizes to minimize waste and save costs.
Pain Point – Inefficient Production Planning and Scheduling:
Manufacturing hair color products requires meticulous planning and coordination to meet market demand. Challenges arise due to the frequent introduction of new colors and products, which can strain production schedules and lead to delays in product release.
Customized ERP Solution:
The ERP system can incorporate advanced production planning and scheduling modules that streamline the manufacturing process. It can help in forecasting demand, balancing resources, and creating optimized production schedules based on real-time data. This ensures that manufacturers can efficiently allocate resources and meet customer demands promptly.
Pain Point – Quality Control and Compliance:
Hair color products must meet stringent quality standards and comply with regulations to ensure consumer safety. Manual quality control processes can be time-consuming, leading to potential errors and inconsistencies.
Customized ERP Solution:
A custom ERP system can include robust quality control modules that track every stage of production, from raw material inspection to the final product. It can implement automated quality checks, reducing the risk of defects and ensuring compliance with industry regulations. Detailed production records can be maintained, aiding in traceability and facilitating recall processes if necessary.
Pain Point – Sales and Distribution Challenges:
Managing sales orders and distribution can become overwhelming for manufacturers, especially when dealing with large volumes of orders from distributors, retailers, and online channels. Order processing delays and inaccuracies can lead to dissatisfied customers and lost sales opportunities.
Customized ERP Solution:
The ERP system can integrate comprehensive sales and distribution modules that automate order processing, invoicing, and shipping. Real-time tracking of orders and inventory levels allows for accurate delivery estimates and minimizes lead times. Improved customer relationship management features enable personalized communication with clients, fostering long-term relationships and repeat business.
See How My Company Can Massively Automate Your Company Departments
Custom CRM Development – For Organizations to manage its Customer Interactions in addition to Sales, Marketing, Billing, Products, Services, Contacts, Customer Support, among other things.
Custom ERP Development – For Manufacturers to handle BOM, Quotation, Order, RFQ, PO, SOA, Manufacturing, Trading, Inventory, Quality Control, Logistics, Shipments, and so on.
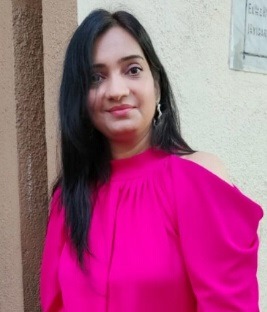
Pain Point – Lack of Real-time Data and Analytics:
Decisions based on outdated or inaccurate data can hinder business growth and strategic planning. Hair color manufacturers require real-time insights into production, sales, and inventory to make informed decisions.
Customized ERP Solution:
A tailored ERP system can incorporate advanced analytics and reporting tools that provide real-time data visualization. Manufacturers can access key performance indicators (KPIs) related to production efficiency, sales trends, and inventory turnover, empowering them to make data-driven decisions that enhance overall operational efficiency and profitability.
Conclusion
In the fast-paced and competitive world of hair color manufacturing, having a customized ERP system can significantly transform business operations. By addressing pain points related to inventory management, production planning, quality control, sales, and data analytics, the ERP solution can streamline processes, reduce costs, and improve overall customer satisfaction. With a comprehensive ERP system built specifically for their unique needs, hair color manufacturers can confidently navigate the challenges of the industry and thrive in a dynamic market.
Use Case: Streamlining Hair Color Manufacturing with Customized ERP
Optimizing Production Efficiency and Customer Satisfaction in Hair Color Manufacturing
The following use case illustrates how a customized ERP system for hair color manufacturing can transform the business operations of a fictional company called “ColorTrends Inc.” The ERP solution addresses pain points faced by the company, resulting in improved production efficiency, streamlined inventory management, and enhanced customer satisfaction.
1. Scenario: Efficient Inventory Management
Pain Point:
ColorTrends Inc. struggled to manage its diverse inventory of raw materials, color pigments, and packaging. Frequent stockouts and overstocking led to production delays and increased costs.
Solution:
The customized ERP system integrated by ColorTrends Inc. offers real-time inventory tracking. Automated reorder points and stock alerts are set up to ensure that the company is promptly notified when stock levels are low. The ERP also provides a comprehensive view of inventory, allowing ColorTrends Inc. to optimize batch sizes, minimize waste, and reduce overall production costs.
2. Scenario: Streamlined Production Planning and Scheduling
Pain Point:
The company faced challenges in planning and scheduling production, especially with the introduction of new colors and products. This led to inefficiencies and delays in meeting market demand.
Solution:
The ERP system’s advanced production planning and scheduling modules aid ColorTrends Inc. in forecasting demand accurately. Based on real-time data, the system creates optimized production schedules that balance resources and prioritize high-demand products. With the ERP’s assistance, the company can efficiently allocate resources, improve production timelines, and respond quickly to changing market trends.
3. Scenario: Enhanced Quality Control and Compliance
Pain Point:
Manual quality control processes at ColorTrends Inc. were time-consuming and prone to errors, potentially compromising product quality and compliance with safety regulations.
Solution:
The ERP system integrates robust quality control modules that track every stage of the production process. Automated quality checks ensure consistency and compliance with industry regulations. The system maintains detailed production records, enabling traceability and facilitating prompt recalls, if needed, to maintain consumer safety and uphold the company’s reputation for quality products.
4. Scenario: Streamlined Sales and Distribution
Pain Point:
ColorTrends Inc. struggled with managing sales orders and distribution, leading to delays and inaccuracies in order processing, ultimately affecting customer satisfaction.
Solution:
The ERP system incorporates comprehensive sales and distribution modules that automate order processing, invoicing, and shipping. Real-time tracking of orders and inventory levels allows the company to provide accurate delivery estimates and reduce lead times. With improved customer relationship management features, ColorTrends Inc. can offer personalized communication with clients, ensuring better customer satisfaction and loyalty.
5. Scenario: Real-time Data Insights and Analytics
Pain Point:
Lack of real-time data and analytics hindered ColorTrends Inc.’s ability to make informed decisions promptly, potentially affecting business growth.
Solution:
The ERP system includes advanced analytics and reporting tools that offer real-time data visualization. Key performance indicators related to production efficiency, sales trends, and inventory turnover are readily available. Armed with valuable insights, ColorTrends Inc. can make data-driven decisions, optimize business operations, and identify new opportunities for growth.
Conclusion
By implementing a customized ERP system, ColorTrends Inc. successfully addresses its pain points related to inventory management, production planning, quality control, sales, and data analytics. The ERP solution transforms the company’s operations. It streamlines processes, reduces costs, and enhances customer satisfaction. With increased efficiency and better decision-making capabilities, ColorTrends Inc. establishes itself as a leader in the hair color manufacturing industry. The company thrives in a competitive market.