Scalp Care Product Manufacturing ERP
Scalp care products have witnessed a surge in demand as consumers become more conscious of their hair and scalp health. For manufacturers in this industry, meeting this growing demand while maintaining quality, accuracy, and efficiency in production can be a daunting challenge. Manual processes, inventory mismanagement, and lack of real-time data often lead to bottlenecks and hinder business growth. To overcome these pain points, a customized Scalp Care Product Manufacturing ERP system can be the perfect solution.
Pain Points and Solutions
Pain Point – Complex Production Processes
Manufacturing scalp care products involves a complex series of tasks, from recipe formulation to batch production. The absence of a streamlined process can lead to inefficiencies, errors in mixing ingredients, and ultimately, subpar products. This can negatively impact brand reputation and customer loyalty.
Customized ERP Solution:
A tailor-made ERP can provide step-by-step production workflows, ensuring consistency and accuracy throughout the manufacturing process. It enables manufacturers to create and maintain standard operating procedures (SOPs) for each product, reducing the risk of human errors and ensuring product quality remains consistent.
Pain Point – Ingredient Inventory Management
Tracking ingredients and raw materials is crucial in scalp care product manufacturing. Without real-time visibility into inventory levels, manufacturers may face production delays, overstocking, or stockouts, leading to increased costs and missed sales opportunities.
Customized ERP Solution:
A customized ERP can offer a centralized inventory management system that monitors ingredient levels in real-time. Automated alerts can notify manufacturers when inventory reaches a defined threshold, facilitating timely reordering and preventing production interruptions.
Pain Point – Formulation Accuracy
Formulating scalp care products requires precision, as even small discrepancies can lead to undesirable results. Without proper formulation management, manufacturers may struggle to maintain consistency across batches, leading to wastage and increased production costs.
Customized ERP Solution:
A customized ERP can store and manage formulation data, enabling manufacturers to access accurate recipes and ingredient quantities for each product. By utilizing ERP’s batch management capabilities, manufacturers can precisely replicate successful formulas, thereby ensuring consistency in product quality and minimizing wastage.
See How My Company Can Massively Automate Your Company Departments
Custom CRM Development – For Organizations to manage its Customer Interactions in addition to Sales, Marketing, Billing, Products, Services, Contacts, Customer Support, among other things.
Custom ERP Development – For Manufacturers to handle BOM, Quotation, Order, RFQ, PO, SOA, Manufacturing, Trading, Inventory, Quality Control, Logistics, Shipments, and so on.
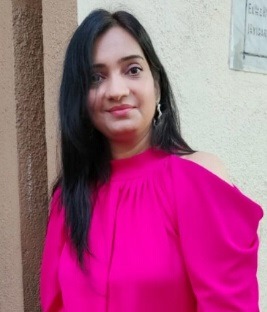
Pain Point – Packaging and Labeling Compliance
Complying with packaging and labeling regulations is crucial for scalp care product manufacturers. Failure to meet these requirements can lead to fines, product recalls, and damage to brand reputation.
Customized ERP Solution:
A customized ERP can integrate labeling and packaging compliance standards into the production process. By automating label generation based on product specifications, manufacturers can ensure that each product package contains accurate and compliant information, mitigating the risk of regulatory non-compliance.
Pain Point – Lack of Real-time Data for Informed Decision-making
In a dynamic industry like scalp care product manufacturing, having access to real-time data is essential for making informed business decisions. Manual data collection and analysis can be time-consuming, leaving manufacturers with outdated information and hampering strategic planning.
Customized ERP Solution:
A customized ERP can provide real-time data analytics and reporting capabilities. Manufacturers can monitor key performance indicators (KPIs), such as production output, sales trends, and inventory levels, allowing them to make data-driven decisions promptly. These insights can help manufacturers identify areas of improvement, optimize production, and respond quickly to market demands.
Conclusion
For scalp care product manufacturers, a customized ERP solution can be a game-changer in streamlining operations and addressing critical pain points. By implementing an ERP system tailored to the unique needs of the industry, manufacturers can improve production efficiency, ensure product quality, and stay compliant with regulations. Real-time data access empowers decision-makers to make informed choices, fostering business growth and enhancing customer satisfaction. Embracing the power of ERP technology can position scalp care product manufacturers at the forefront of the industry, ready to meet the demands of a thriving market.
Use Case: Optimizing Scalp Care Product Manufacturing with Customized ERP
XYZ Scalp Care Products Inc. Enhances Efficiency and Quality with Tailor-Made ERP
XYZ Scalp Care Products Inc. is a leading manufacturer of high-quality scalp care products, catering to an ever-growing market of health-conscious consumers. To maintain their competitive edge and meet the rising demand, the company faced the challenge of streamlining their production processes, managing inventory effectively, and ensuring accurate formulations. They decided to implement a customized Enterprise Resource Planning (ERP) system to address these pain points and achieve operational excellence.
XYZ Scalp Care Products Inc. faced the following challenges
Complex Production Processes:
The company’s production workflow lacked standardization, resulting in inconsistencies and occasional formulation errors. This led to a waste of valuable ingredients and compromised product quality.
Ingredient Inventory Management:
The company struggled with manual tracking of ingredient inventory, leading to stockouts and delayed production due to sudden shortages.
Formulation Accuracy:
Without a centralized repository for formulations and SOPs, the R&D team found it difficult to maintain consistent product quality across batches.
Packaging and Labeling Compliance:
The regulatory landscape for packaging and labeling was ever-evolving, making it challenging for XYZ Scalp Care Products Inc. to ensure compliance for each product variant.
Lack of Real-time Data:
Decision-makers lacked access to real-time data, making it challenging to respond promptly to market changes and optimize production schedules.
Implementation of Customized ERP Solution
To overcome these challenges, XYZ Scalp Care Products Inc. partnered with a specialized ERP solution provider to develop a customized system tailored to their specific needs.
Streamlined Production Processes:
The ERP system was designed to include step-by-step production workflows based on industry best practices. Each product’s formulation, mixing instructions, and quality control checkpoints were documented in the ERP system. This ensured that every production run followed the correct procedures, minimizing errors and enhancing product consistency.
Ingredient Inventory Management:
The ERP system integrated with the company’s inventory database, providing real-time visibility into ingredient levels. Automated alerts were set up to notify the procurement team when stock levels fell below a predefined threshold. This allowed the team to initiate purchase orders promptly, ensuring a steady supply of raw materials and preventing production delays.
Formulation Accuracy:
The ERP system implemented a centralized repository for formulation data and SOPs. The R&D team could now access standardized formulations and mixing instructions, minimizing variations between batches and reducing material waste. The system also facilitated collaboration among team members during the formulation process, promoting knowledge sharing and innovation.
Packaging and Labeling Compliance:
The ERP system incorporated the latest regulatory standards for packaging and labeling. As soon as a new product variant was created, the system automatically generated compliant labels and packaging specifications. This eliminated the risk of non-compliance and streamlined the product release process.
Real-time Data Access:
The ERP system provided real-time analytics and reporting capabilities, accessible to key decision-makers across the organization. Dashboards displayed crucial KPIs such as production output, sales figures, and inventory levels. This empowered the management team to make data-driven decisions, respond quickly to changing market demands, and identify areas for continuous improvement.
Results and Benefits
By implementing the customized ERP system, XYZ Scalp Care Products Inc. experienced significant improvements in their manufacturing processes and overall business operations:
Enhanced Product Quality:
The standardization of production workflows and formulation data resulted in consistent and high-quality scalp care products, increasing customer satisfaction and brand loyalty.
Efficient Inventory Management:
Real-time inventory monitoring and automated alerts reduced stockouts, ensuring uninterrupted production and optimizing inventory levels, thus minimizing carrying costs.
Regulatory Compliance:
The ERP’s automated labeling and packaging compliance features ensured that each product adhered to the latest regulatory requirements, eliminating the risk of fines or product recalls.
Informed Decision-making:
Real-time data access empowered the management team to make timely and strategic decisions, enabling proactive responses to market trends and opportunities.
Improved Efficiency:
The ERP system streamlined various processes, saving time and resources, and enabling the company to focus on product innovation and market expansion.
Conclusion
The implementation of a customized ERP system was a game-changer for XYZ Scalp Care Products Inc. It integrated production workflows, inventory management, and formulation data. Real-time analytics enhanced their manufacturing efficiency and product quality. Overall business performance improved significantly. By leveraging ERP technology, XYZ Scalp Care Products Inc. cemented its position as a leading manufacturer of scalp care products. They met customer needs and adapted swiftly to the ever-evolving market demands.