Custom ERP for Electric Skillet Manufacturers: Enhance Efficiency
The electric skillet manufacturing industry is experiencing rapid growth, driven by the increasing demand for versatile and convenient cooking solutions. However, amidst this growth, businesses in the sector face several pain points that hinder their efficiency and profitability. In this article, we explore the challenges faced by electric skillet manufacturers and demonstrate how a customized Enterprise Resource Planning (ERP) solution can alleviate these pain points, leading to improved operational effectiveness and business success.
Pain Points and Custom ERP Solutions
Complex Inventory Management
Pain Point:
One of the primary challenges faced by electric skillet manufacturers is the management of inventory. With multiple components, parts, and variations in skillet models, maintaining accurate inventory levels can be a daunting task. This complexity often results in inefficiencies, stockouts, and overstocking, leading to increased costs and customer dissatisfaction.
Customized ERP Solution:
A tailored ERP system provides real-time visibility into inventory levels, enabling manufacturers to monitor stock levels accurately. It automates inventory tracking, streamlines purchase orders, and facilitates automated reordering based on predefined stock thresholds. Additionally, ERP analytics can forecast demand patterns, allowing manufacturers to optimize inventory levels and minimize wastage.
Inefficient Production Planning
Pain Point:
Effective production planning is crucial for electric skillet manufacturers to meet customer demands, reduce lead times, and optimize resource utilization. However, manual planning processes and lack of integration between departments often result in production bottlenecks, delays, and increased costs.
Customized ERP Solution:
A customized ERP system centralizes production planning, integrating data from various departments such as sales, inventory, and manufacturing. It enables manufacturers to create accurate production schedules, taking into account real-time inventory levels, order volumes, and resource availability. By automating workflows and providing visibility into production processes, ERP improves coordination, reduces delays, and enhances overall operational efficiency.
Inadequate Supplier Management
Pain Point:
Electric skillet manufacturers rely on a network of suppliers for sourcing raw materials and components. However, managing multiple suppliers, negotiating contracts, and ensuring timely deliveries can be challenging, leading to supply chain disruptions and quality issues.
Customized ERP Solution:
A tailored ERP solution streamlines supplier management processes by providing a centralized platform for supplier communication, contract management, and performance tracking. Consequently, it enables manufacturers to maintain a comprehensive supplier database, compare quotes, and manage purchase orders efficiently. With real-time visibility into supplier performance metrics, manufacturers can easily identify underperforming suppliers, negotiate better terms, and maintain consistent quality standards. Thus, the ERP solution significantly enhances the overall efficiency and effectiveness of supplier management.
Manual Procurement Processes
Pain Point:
Manual procurement processes, such as raising purchase requests, obtaining approvals, and tracking purchases, are time-consuming and prone to errors. These inefficiencies can lead to delays in procuring critical components, impacting production timelines and customer satisfaction.
Customized ERP Solution:
A customized ERP system automates the procurement process, from requisition to payment. Firstly, it enables manufacturers to create purchase requisitions electronically. Then, it routes them for approval based on predefined workflows and subsequently generates purchase orders automatically. By digitizing procurement processes, the ERP system significantly reduces paperwork, eliminates errors, and ensures the timely procurement of required materials. Consequently, manufacturers can enjoy a more efficient and streamlined procurement process.
See How My Company Can Massively Automate Your Company Departments
Custom CRM Development – For Organizations to manage its Customer Interactions in addition to Sales, Marketing, Billing, Products, Services, Contacts, Customer Support, among other things.
Custom ERP Development – For Manufacturers to handle BOM, Quotation, Order, RFQ, PO, SOA, Manufacturing, Trading, Inventory, Quality Control, Logistics, Shipments, and so on.
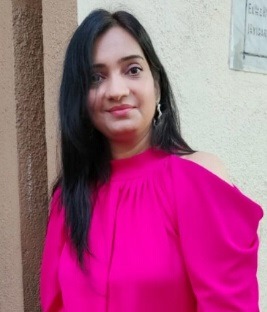
Lack of Data-driven Decision Making
Pain Point:
Electric skillet manufacturers often struggle with making informed decisions due to a lack of real-time data and insights. Without access to accurate information, businesses may face challenges in identifying trends, optimizing resources, and improving overall performance.
Customized ERP Solution:
A tailored ERP solution integrates data from various departments and processes, providing comprehensive analytics and insights. Manufacturers can leverage real-time dashboards, reports, and predictive analytics to monitor key performance indicators (KPIs), identify bottlenecks, and make data-driven decisions. Whether it’s identifying popular skillet models, forecasting demand, or optimizing production schedules, ERP empowers manufacturers to drive continuous improvement and stay ahead of market trends.
Conclusion
Customized ERP solutions have the potential to revolutionize the electric skillet manufacturing industry by effectively addressing the pain points that hinder efficiency and profitability. By streamlining inventory management, production planning, supplier management, and procurement processes, as well as enabling data-driven decision making, ERP empowers manufacturers to optimize operations. Consequently, they can reduce costs and enhance customer satisfaction. Therefore, embracing a tailored ERP solution is the key to staying competitive in the dynamic and evolving landscape of electric skillet manufacturing.
Use Case: Streamlining Production and Inventory with Custom ERP for Electric Skillet Manufacturing
ABC Electric Skillets is a leading manufacturer of high-quality electric skillets. With a diverse product range and increasing customer demand, ABC Electric Skillets faced challenges in managing production planning and inventory effectively. They recognized the need for an integrated solution to streamline their operations and enhance overall efficiency. They decided to implement a customized Enterprise Resource Planning (ERP) system to address their pain points and transform their manufacturing processes.
Challenge
ABC Electric Skillets struggled with manual production planning processes, resulting in delays, resource inefficiencies, and increased costs. They faced difficulties in aligning production schedules with real-time inventory levels and customer demands. Additionally, the lack of visibility into their inventory led to stockouts, overstocking, and challenges in fulfilling orders on time.
Solution: Implementing Customized ERP for Electric Skillet Manufacturing
Streamlined Production Planning
By implementing a customized ERP solution, ABC Electric Skillets gained the ability to centralize their production planning processes. The ERP system integrated data from various departments, including sales, inventory, and manufacturing. This integration allowed them to create accurate production schedules based on real-time inventory levels, order volumes, and resource availability. Automated workflows and notifications enabled seamless coordination between different teams, reducing delays and enhancing overall production efficiency.
Real-time Inventory Management
The ERP system provided ABC Electric Skillets with real-time visibility into their inventory levels. They could track stock movements, monitor raw material availability, and identify shortages or excesses promptly. With automated alerts and notifications, the ERP system ensured that the procurement team was notified when inventory levels reached predefined thresholds, enabling proactive reordering of raw materials and components. This streamlined approach eliminated stockouts and overstocking, reducing carrying costs and optimizing inventory levels.
Demand Forecasting and Planning
The ERP solution incorporated advanced analytics capabilities, allowing ABC Electric Skillets to leverage historical sales data, market trends, and customer insights for demand forecasting. By analyzing patterns and trends, they could accurately anticipate customer demands and adjust production plans accordingly. This proactive approach helped them optimize resource allocation, minimize lead times, and ensure on-time delivery of skillets to customers.
Supplier Management and Procurement Automation
With the customized ERP system, ABC Electric Skillets transformed their supplier management and procurement processes. They created a centralized supplier database, including information on pricing, lead times, and quality performance. This allowed them to compare supplier quotes, negotiate better terms, and make informed decisions while selecting suppliers. The ERP system automated the procurement workflow, from raising purchase requisitions to generating purchase orders, eliminating manual paperwork and reducing errors. These streamlined processes ensured timely procurement of raw materials and components, supporting uninterrupted production schedules.
Enhanced Data-driven Decision Making
The ERP system provided ABC Electric Skillets with real-time dashboards, reports, and analytics, thereby enabling data-driven decision making. Consequently, they could monitor key performance indicators (KPIs) such as production output, inventory turnover, and order fulfillment rates. With comprehensive insights into their operations, they could easily identify bottlenecks, track performance against targets, and make informed decisions to drive continuous improvement. Furthermore, data-driven decision making helped them optimize resource allocation, identify popular skillet models, and align production plans with market demands.
Results and Benefits
By implementing a customized ERP system, ABC Electric Skillets achieved significant improvements in their electric skillet manufacturing processes:
Improved Production Efficiency:
Streamlined production planning and resource allocation reduced lead times and minimized production bottlenecks, resulting in increased operational efficiency.
Optimized Inventory Management:
Real-time visibility into inventory levels and demand forecasting capabilities reduced stockouts and overstocking, optimizing inventory levels and reducing carrying costs.
Efficient Supplier Management:
Centralized supplier management and automated procurement processes improved supplier selection, reduced procurement lead times, and ensured timely availability of raw materials and components.
Enhanced Decision Making:
Data-driven insights and analytics enabled ABC Electric Skillets to make informed decisions, driving continuous improvement and staying ahead of market trends.
Customer Satisfaction:
Improved production planning and inventory management resulted in faster order fulfillment, on-time deliveries, and improved customer satisfaction.
Conclusion
By leveraging a customized ERP solution, ABC Electric Skillets successfully addressed their pain points related to production planning and inventory management. Firstly, the integrated system streamlined their manufacturing processes. Additionally, it optimized resource allocation, improved inventory control, and empowered data-driven decision making. Consequently, ABC Electric Skillets achieved increased operational efficiency, reduced costs, and enhanced customer satisfaction. Ultimately, the use of a tailored ERP solution proved to be instrumental in transforming their electric skillet manufacturing business into a more agile and competitive enterprise.