ERP for Electric Popcorn Cart Manufacturers: Automate Production
Electric popcorn cart manufacturing businesses have been thriving in recent years, thanks to the growing demand for freshly popped popcorn at various events and venues. However, with this increasing popularity comes a set of unique challenges that can hinder operational efficiency and profitability. This article explores the pain points faced by electric popcorn cart manufacturers and how a customized Enterprise Resource Planning (ERP) software can alleviate these challenges, resulting in streamlined operations and improved business performance.
Pain Points
Inefficient Production Scheduling:
One major pain point for electric popcorn cart manufacturers is the lack of an efficient production scheduling system. Without proper planning and coordination, there is a risk of overproduction or underproduction, leading to wastage of resources and missed opportunities to meet customer demands. A customized ERP solution can address this challenge by providing a centralized platform that integrates production planning, inventory management, and sales data. This enables real-time visibility into production schedules, allowing manufacturers to optimize production capacity, allocate resources effectively, and ensure timely delivery of orders.
Complex Inventory Control:
Managing inventory can be a daunting task for electric popcorn cart manufacturers. With multiple ingredients, packaging materials, and equipment to track, it becomes difficult to maintain accurate inventory levels and prevent stockouts or excess stock. A customized ERP system can simplify inventory control by automating inventory tracking, enabling manufacturers to monitor stock levels, set up reorder points, and generate purchase orders automatically when inventory reaches a certain threshold. This ensures that the right materials are available at the right time, minimizing stockouts and reducing carrying costs.
Manual Order Processing:
Manual order processing can be time-consuming and error-prone, leading to delays in order fulfillment and dissatisfied customers. An integrated ERP solution can streamline the order processing workflow by automating order capture, verification, and fulfillment processes. With a centralized system, manufacturers can easily track orders, generate invoices, and manage shipping and delivery, resulting in faster order processing and improved customer satisfaction.
Supplier Management and Procurement Challenges:
Dealing with multiple suppliers for various raw materials and equipment can be a complex task. Coordinating with different vendors, managing procurement timelines, and ensuring quality standards can be overwhelming for electric popcorn cart manufacturers. A customized ERP software can simplify supplier management and procurement processes by providing a centralized supplier database, automating purchase order generation, and facilitating communication with suppliers. This streamlines procurement activities, reduces lead times, improves supplier relationships, and enhances overall supply chain efficiency.
Lack of Sales Analytics:
Understanding sales trends and customer preferences is crucial for making informed business decisions. However, without comprehensive analytics, it can be challenging for electric popcorn cart manufacturers to gain insights into their sales performance. A customized ERP system can address this pain point by providing robust reporting and analytics capabilities. Manufacturers can analyze sales data, identify popular popcorn flavors or packaging options, and forecast demand more accurately. This enables proactive decision-making, such as adjusting production volumes, introducing new flavors, or targeting specific customer segments, ultimately maximizing sales and profitability.
See How My Company Can Massively Automate Your Company Departments
Custom CRM Development – For Organizations to manage its Customer Interactions in addition to Sales, Marketing, Billing, Products, Services, Contacts, Customer Support, among other things.
Custom ERP Development – For Manufacturers to handle BOM, Quotation, Order, RFQ, PO, SOA, Manufacturing, Trading, Inventory, Quality Control, Logistics, Shipments, and so on.
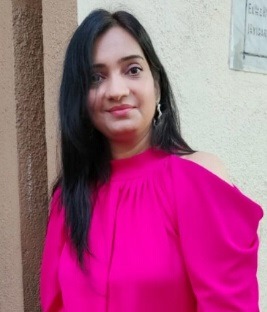
Conclusion
Electric popcorn cart manufacturers face several pain points in managing their operations efficiently. However, by implementing a customized ERP solution, these challenges can be effectively addressed. From streamlining production scheduling and inventory control to simplifying order processing and procurement, an ERP system provides a comprehensive framework for managing all aspects of the business. By harnessing the power of data analytics, manufacturers can gain valuable insights into sales trends and optimize their operations for enhanced profitability. Embracing technology through a customized ERP solution is the key to unlocking the full potential of electric popcorn cart manufacturing businesses in the dynamic and competitive market.
Use Case: Optimizing Production and Inventory Management with ERP for Electric Popcorn Cart Manufacturing
Company Profile:
ABC Electric Popcorn Carts is a leading manufacturer of high-quality electric popcorn carts catering to various events, fairs, and venues. With a wide range of flavors and customizable packaging options, ABC Electric Popcorn Carts has gained a reputation for delivering freshly popped popcorn that satisfies even the most discerning taste buds.
Challenge
As ABC Electric Popcorn Carts experienced rapid growth, they faced numerous operational challenges that hindered their ability to meet customer demands efficiently. Their manual processes for production scheduling, inventory control, and order processing were time-consuming, error-prone, and led to inefficiencies in their supply chain. They needed a solution that could streamline their operations, enhance inventory management, and provide real-time insights into their sales and production data.
Implementing a Customized ERP System
ABC Electric Popcorn Carts decided to invest in a customized Enterprise Resource Planning (ERP) system specifically tailored to their unique needs. The ERP system integrated all aspects of their business, providing a centralized platform for managing production, inventory, and sales. Here’s how the ERP solution resolved their pain points:
Streamlining Production Scheduling:
The ERP system enabled ABC Electric Popcorn Carts to optimize their production schedules by automating and centralizing the process. Production planners could easily create and adjust production schedules based on real-time data. It ensures efficient resource allocation and timely order fulfillment. The system also facilitated communication between the production team and other departments. It helped in enhancing collaboration and reducing the risk of miscommunication or delays.
Enhancing Inventory Control:
With the ERP system’s inventory management module, ABC Electric Popcorn Carts gained better control over their inventory levels. The system automatically tracked inventory in real-time, enabling accurate forecasting and preventing stockouts or excess stock. By setting up reorder points and automated purchase order generation, the company could maintain optimal inventory levels, minimize carrying costs, and ensure that the required ingredients and packaging materials were always available when needed.
Automating Order Processing:
The ERP system streamlined the order processing workflow, eliminating manual errors and delays. As orders were captured electronically, the system automatically verified the details and triggered the fulfillment process. Invoices were generated promptly, and shipping and delivery information was seamlessly communicated to the logistics team. This automation not only accelerated order processing but also improved customer satisfaction. All this only by providing timely updates on order status and delivery.
Simplifying Supplier Management and Procurement:
The ERP system simplified supplier management and procurement processes for ABC Electric Popcorn Carts. The company could maintain a centralized supplier database, track supplier performance, and manage contracts effectively. With automated purchase order generation based on inventory levels, procurement became more efficient and streamlined. The system also facilitated communication with suppliers, enabling seamless collaboration and timely delivery of raw materials and equipment.
Utilizing Sales Analytics:
The ERP system provided ABC Electric Popcorn Carts with valuable sales analytics, allowing them to make data-driven decisions. With real-time access to sales data, the company could identify popular popcorn flavors, packaging options, and customer preferences. This insight helped them optimize their production volumes, introduce new flavors based on market trends, and target specific customer segments more effectively. By aligning their production and marketing strategies with customer demands, ABC Electric Popcorn Carts increased sales and improved profitability.
Results
By implementing the customized ERP system, ABC Electric Popcorn Carts experienced significant improvements in their operations and overall business performance. They achieved:
- Streamlined production scheduling, leading to optimized resource allocation and on-time order fulfillment.
- Enhanced inventory control, reducing stockouts and minimizing carrying costs.
- Accelerated order processing, resulting in improved customer satisfaction.
- Simplified supplier management and procurement processes, ensuring timely delivery of materials.
- Data-driven decision-making through sales analytics, maximizing sales and profitability.
With the ERP system as a solid foundation, ABC Electric Popcorn Carts achieved operational efficiency. This streamlined their supply chain, and positioned themselves for continued growth in the competitive electric popcorn cart manufacturing industry.