ERP for Electric Pancake Maker Manufacturers: Reducing Cost
The electric pancake maker manufacturing industry has experienced significant growth and demand in recent years. As this sector expands, so do the challenges faced by manufacturers. In order to stay competitive and efficient, businesses must address various pain points such as inventory management, production planning, order fulfillment, supplier management, and demand forecasting. A customized Enterprise Resource Planning (ERP) solution offers a comprehensive approach to resolving these pain points, enabling electric pancake maker manufacturers to optimize their operations and provide delicious and evenly cooked pancakes to their customers.
Pain Points
Inventory Management:
Effective inventory management is crucial for electric pancake maker manufacturers. Maintaining an optimal balance between raw materials, work-in-progress (WIP), and finished goods is essential to meet customer demands while minimizing costs and wastage. A customized ERP system can provide real-time visibility into inventory levels, enabling manufacturers to track stock, identify low levels, and automate reorder processes. With accurate inventory data, businesses can avoid stockouts, reduce excess inventory, and ensure timely production and order fulfillment.
Production Planning:
Efficient production planning is vital to meet customer expectations and optimize resources. Traditional manual planning processes can be time-consuming, error-prone, and lack agility. A customized ERP solution streamlines production planning by automating scheduling, optimizing machine and labor allocation, and providing real-time visibility into production progress. By aligning production with demand forecasts, manufacturers can optimize their production schedules, minimize idle time, reduce lead times, and enhance overall productivity.
Order Fulfillment:
Timely order fulfillment is a critical aspect of customer satisfaction. Electric pancake maker manufacturers often face challenges in managing complex order workflows, tracking orders, and ensuring on-time delivery. A customized ERP system enables businesses to automate the entire order fulfillment process, from order placement to delivery. Manufacturers can monitor order status, track inventory availability, allocate resources efficiently, and generate accurate shipping and delivery schedules. This level of automation and visibility helps eliminate errors, reduce delays, improve customer satisfaction, and build long-term relationships with clients.
Supplier Management and Procurement:
Maintaining strong relationships with suppliers and ensuring a smooth procurement process is essential for electric pancake maker manufacturers. Manual supplier management and procurement processes can be time-consuming, prone to errors, and lack transparency. A customized ERP solution facilitates streamlined supplier management by automating procurement workflows, centralizing supplier data, and providing real-time visibility into supplier performance and inventory availability. By optimizing the procurement process, manufacturers can reduce costs, negotiate better terms with suppliers, minimize stockouts, and improve overall supply chain efficiency.
Demand Forecasting and Analytics:
Accurate demand forecasting is critical for electric pancake maker manufacturers to avoid overstocking or understocking inventory. Traditional forecasting methods often lack precision and fail to adapt to changing market trends. A customized ERP system incorporates advanced analytics and machine learning algorithms to analyze historical data, market trends, and customer behavior. By leveraging this data, manufacturers can generate accurate demand forecasts, optimize inventory levels, identify opportunities for product innovation, and make informed business decisions.
See How My Company Can Massively Automate Your Company Departments
Custom CRM Development – For Organizations to manage its Customer Interactions in addition to Sales, Marketing, Billing, Products, Services, Contacts, Customer Support, among other things.
Custom ERP Development – For Manufacturers to handle BOM, Quotation, Order, RFQ, PO, SOA, Manufacturing, Trading, Inventory, Quality Control, Logistics, Shipments, and so on.
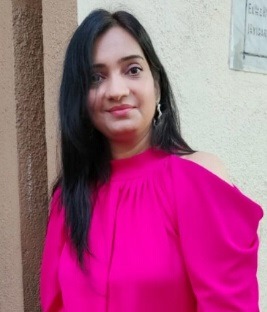
Conclusion
The electric pancake maker manufacturing industry faces various pain points that can be effectively addressed through a customized ERP solution. By streamlining inventory management, production planning, order fulfillment, supplier management, and demand forecasting, manufacturers can optimize their operations and deliver delicious and evenly cooked pancakes to their customers. Embracing a tailored ERP system empowers businesses to enhance efficiency, reduce costs, improve customer satisfaction, and gain a competitive edge in this rapidly growing market.
Use Case: Optimizing Operations for Electric Pancake Maker Manufacturing with Customized ERP
Company Background:
Pancake Delights is a prominent manufacturer of electric pancake makers, catering to a wide range of customers globally. With their commitment to quality and innovative designs, they have experienced substantial growth in recent years. However, as the business expanded, they encountered operational challenges that hindered their ability to meet customer demands efficiently. To address these pain points, Pancake Delights decided to implement a customized Enterprise Resource Planning (ERP) solution.
Pain Points
Inventory Management:
Pancake Delights struggled with inventory management due to a lack of visibility into stock levels and inaccurate forecasting. This resulted in frequent stockouts and excess inventory, leading to increased costs and delayed production.
Production Planning:
The manual production planning process was time-consuming and prone to errors. As a result, Pancake Delights faced challenges in meeting fluctuating customer demands, resulting in missed deadlines and dissatisfied customers.
Order Fulfillment:
The existing order fulfillment process lacked automation and real-time tracking, leading to delayed deliveries and poor customer satisfaction. Pancake Delights needed a system that could streamline the order workflow and provide visibility into order status and inventory availability.
Supplier Management and Procurement:
Procurement processes were decentralized, making it difficult to track supplier performance, negotiate favorable terms, and ensure timely delivery of raw materials. Pancake Delights needed a centralized system to manage suppliers efficiently and optimize procurement.
Demand Forecasting and Analytics:
Lack of accurate demand forecasting hindered Pancake Delights’ ability to plan production schedules and optimize inventory levels. They required an ERP solution that could analyze historical data, market trends, and customer behavior to generate accurate demand forecasts and support data-driven decision-making.
Solution
Customized ERP Implementation Pancake Delights partnered with an ERP provider specializing in the manufacturing industry to implement a tailored ERP solution that addressed their specific pain points.
Inventory Management:
The ERP system provided real-time visibility into inventory levels, enabling Pancake Delights to track stock, automate reorder processes, and minimize stockouts and excess inventory. They could now maintain optimal inventory levels, reducing costs and ensuring timely production.
Production Planning:
Automated production planning within the ERP system enabled Pancake Delights to optimize machine and labor allocation, synchronize production schedules with demand forecasts, and minimize idle time. This resulted in improved production efficiency, reduced lead times, and enhanced customer satisfaction.
Order Fulfillment:
The ERP system streamlined the order fulfillment process by automating order workflows, providing real-time order tracking, and integrating with shipping carriers. Pancake Delights gained complete visibility into order status, inventory availability, and delivery schedules, ensuring on-time deliveries and improving customer satisfaction.
Supplier Management and Procurement:
The centralized ERP solution facilitated seamless supplier management and procurement. Pancake Delights could now automate procurement workflows, track supplier performance, negotiate better terms, and ensure timely delivery of raw materials. This improved supply chain efficiency and reduced costs.
Demand Forecasting and Analytics:
The ERP system incorporated advanced analytics and machine learning algorithms to analyze historical data, market trends, and customer behavior. Pancake Delights could generate accurate demand forecasts, optimize inventory levels, identify new market opportunities, and make data-driven business decisions for sustained growth.
Results
By implementing a customized ERP solution, Pancake Delights successfully addressed their pain points and achieved several benefits:
- Enhanced inventory management, reducing stockouts and excess inventory.
- Improved production planning, minimizing lead times and meeting customer demands more efficiently.
- Streamlined order fulfillment, ensuring on-time deliveries and increasing customer satisfaction.
- Optimized supplier management and procurement, improving supply chain efficiency and reducing costs.
- Accurate demand forecasting and data-driven decision-making for sustainable growth.
Pancake Delights experienced increased operational efficiency, reduced costs, improved customer satisfaction, and gained a competitive edge in the electric pancake maker manufacturing industry. The customized ERP solution proved instrumental in their growth journey and positioned them for continued success.