ERP for Electric Milkshake Mixer Manufacturers: Boost Production
The electric milkshake mixer manufacturing industry has witnessed significant growth in recent years due to the increasing demand for delicious and frothy milkshakes. However, along with this growth comes a range of challenges that can hinder the efficiency and profitability of these businesses. Inefficiencies in inventory management, production planning, order fulfillment, and supplier management can lead to increased costs, delays, and customer dissatisfaction. To overcome these pain points, tailored ERP for Electric Milkshake Mixer Manufacturers offers a comprehensive solution that optimizes operations and drives business success.
Pain Points
Inventory Management:
Maintaining optimal inventory levels is crucial for electric milkshake mixer manufacturers. Inadequate inventory can lead to stockouts and delays in order fulfillment, while excessive inventory ties up capital and increases carrying costs. A customized ERP solution addresses this pain point by implementing robust inventory management features. It enables real-time tracking of inventory levels, streamlines replenishment processes, and automates stock alerts. By providing a holistic view of inventory across multiple locations, the ERP system empowers manufacturers to make data-driven decisions, optimize stock levels, and ensure uninterrupted production and order fulfillment.
Production Planning and Control:
Efficient production planning is vital for electric milkshake mixer manufacturers to meet customer demands promptly. Ineffective planning can result in production delays, increased costs, and missed delivery deadlines. Customized ERP software alleviates these challenges by integrating production planning and control functionalities. The ERP system enables manufacturers to create accurate production schedules, allocate resources efficiently, and monitor progress in real-time. By utilizing historical production data and demand forecasts, the ERP system optimizes production capacity, minimizes downtime, and improves overall productivity.
Order Fulfillment and Customer Satisfaction:
Timely order fulfillment is crucial for customer satisfaction in the electric milkshake mixer manufacturing industry. Inefficient order processing can lead to delays, errors, and unhappy customers. A customized ERP solution streamlines the order fulfillment process by automating order tracking, generating invoices, and facilitating seamless communication with customers. Real-time visibility into order status and inventory availability helps in accurate promise dates, reducing lead times, and ensuring on-time delivery. The ERP system also enhances customer relationship management by capturing customer data, preferences, and purchase history, enabling personalized service and fostering long-term loyalty.
Supplier Management and Procurement:
Reliable suppliers are essential for maintaining consistent product quality and minimizing production disruptions. However, managing multiple suppliers, negotiating contracts, and monitoring deliveries can be a complex and time-consuming process. A customized ERP solution simplifies supplier management and procurement by centralizing supplier information, automating purchase orders, and streamlining the procurement workflow. The ERP system enables efficient supplier selection, tracks supplier performance, and optimizes inventory replenishment. By ensuring timely deliveries, reducing lead times, and negotiating favorable terms, the ERP system helps manufacturers build strong supplier relationships and achieve cost savings.
Analytics and Forecasting:
Accurate demand forecasting and data-driven decision-making are critical for electric milkshake mixer manufacturers. Traditional manual methods often fall short in providing reliable insights into customer preferences, market trends, and inventory optimization. A customized ERP system incorporates advanced analytics capabilities, leveraging historical sales data, market trends, and customer insights to forecast demand accurately. By identifying patterns, anticipating trends, and optimizing inventory levels, the ERP system helps manufacturers reduce costs, prevent stockouts, and maintain high service levels.
See How My Company Can Massively Automate Your Company Departments
Custom CRM Development – For Organizations to manage its Customer Interactions in addition to Sales, Marketing, Billing, Products, Services, Contacts, Customer Support, among other things.
Custom ERP Development – For Manufacturers to handle BOM, Quotation, Order, RFQ, PO, SOA, Manufacturing, Trading, Inventory, Quality Control, Logistics, Shipments, and so on.
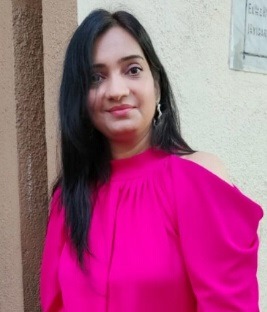
Conclusion
Customized ERP solutions offer electric milkshake mixer manufacturers a comprehensive platform to address pain points and enhance operational efficiency. By streamlining inventory management, production planning, order fulfillment, supplier management, and leveraging advanced analytics, ERP systems empower manufacturers to meet customer demands promptly, minimize costs, and improve overall business performance. With the right ERP solution tailored to their specific needs, electric milkshake mixer manufacturers can achieve a competitive edge, deliver perfectly blended and frothy milkshakes, and drive long-term success in the industry.
Use Case: Streamlining Production and Inventory Management for an Electric Milkshake Mixer Manufacturer
Company Background:
ABC Appliances is a leading manufacturer of electric milkshake mixers, catering to a wide range of customers, including restaurants, cafes, and food service providers. With a growing customer base and expanding product line, ABC Appliances faces challenges in managing its production processes efficiently and optimizing inventory levels. To overcome these pain points, the company decides to implement a customized ERP solution to streamline their operations and drive business growth.
Challenges
Inefficient Production Planning:
ABC Appliances currently relies on manual production planning processes, resulting in frequent bottlenecks, production delays, and increased costs. The lack of real-time visibility into production capacity and resource allocation hampers their ability to meet customer demands promptly.
Disconnected Inventory Management:
The company struggles with maintaining optimal inventory levels across multiple warehouses. Lack of synchronization between inventory data and production schedules often leads to stockouts or excessive inventory, resulting in lost sales and increased carrying costs.
Inaccurate Demand Forecasting:
ABC Appliances lacks reliable insights into market trends, customer preferences, and historical sales data. This hinders their ability to forecast demand accurately, resulting in production inefficiencies, excess inventory, or stockouts.
Manual Order Fulfillment:
The manual order fulfillment process is time-consuming and prone to errors. The lack of a centralized system for order tracking, invoice generation, and customer communication leads to delays in order processing and dissatisfied customers.
Implementing a Customized ERP System
ABC Appliances partners with an ERP solution provider to implement a customized ERP system tailored to their specific needs. The ERP system addresses their pain points and provides the following features:
Integrated Production Planning:
The ERP system enables ABC Appliances to create accurate production schedules based on demand forecasts, available resources, and historical data. Real-time visibility into production progress and resource allocation allows proactive adjustments, minimizing bottlenecks and optimizing production efficiency.
Streamlined Inventory Management:
The ERP system centralizes inventory data across multiple warehouses, providing a holistic view of stock levels, incoming shipments, and production requirements. Real-time inventory tracking and automated alerts ensure timely replenishment, preventing stockouts and reducing excess inventory.
Advanced Demand Forecasting:
Leveraging advanced analytics capabilities, the ERP system analyzes historical sales data, market trends, and customer insights to generate accurate demand forecasts. This empowers ABC Appliances to optimize inventory levels, adjust production capacity, and meet customer demands with precision.
Automated Order Fulfillment:
The ERP system automates the order fulfillment process by integrating order tracking, invoice generation, and communication with customers. Real-time visibility into order status, inventory availability, and automated notifications enable faster order processing, on-time deliveries, and improved customer satisfaction.
Benefits and Outcomes
Enhanced Production Efficiency:
With the ERP system, ABC Appliances experiences streamlined production planning, reducing bottlenecks and improving overall efficiency. Proactive resource allocation and real-time monitoring enable timely adjustments, optimizing production capacity and reducing costs.
Optimized Inventory Management:
The ERP system provides accurate inventory data and automated replenishment processes. ABC Appliances can maintain optimal inventory levels, reducing stockouts, and minimizing carrying costs.
Accurate Demand Forecasting:
Leveraging advanced analytics, the ERP system enables ABC Appliances to forecast demand accurately. This helps in aligning production capacity, reducing excess inventory, and preventing stockouts, resulting in cost savings and improved customer satisfaction.
Improved Order Fulfillment:
The automated order fulfillment process ensures faster order processing, on-time deliveries, and reduced errors. Real-time order tracking and streamlined communication enhance customer satisfaction and strengthen relationships.
Conclusion
ABC Appliances implements a customized ERP for Electric Milkshake Mixer Manufacturers. This helps overcome their pain points and achieve operational excellence. The ERP system streamlines production planning. It optimizes inventory management and enables accurate demand forecasting. Automated order fulfillment empowers efficient customer demand fulfillment, reducing costs and enhancing overall business performance. The ERP system acts as a growth catalyst, solidifying ABC Appliances’ position as a leading provider of high-quality electric milkshake mixers.