ERP for Electric Fondue Set Manufacturers: Maximize Production
In today’s highly competitive market, electric fondue set manufacturers face numerous challenges in streamlining their operations to meet customer demands efficiently. To address these pain points, a tailored Enterprise Resource Planning (ERP) system can revolutionize the manufacturing process by integrating key functions and enabling data-driven decision-making. In this article, we will explore the pain points faced by electric fondue set manufacturers and delve into how a customized ERP solution can effectively resolve these challenges.
Pain Points
Inefficient Production Planning and Management:
One of the primary pain points in electric fondue set manufacturing is inefficient production planning and management. Traditional methods often rely on manual processes and spreadsheets, leading to inaccuracies, delays, and missed deadlines. A customized ERP system can streamline production planning by automating workflows, optimizing resource allocation, and synchronizing production schedules. Real-time data integration allows manufacturers to gain visibility into the production process, leading to improved efficiency, reduced lead times, and better resource utilization.
Lack of Inventory Control:
Maintaining optimal inventory levels is critical for electric fondue set manufacturers. Overstocking can tie up valuable capital and warehouse space, while understocking can result in production delays and missed sales opportunities. A customized ERP solution enables real-time tracking of inventory levels, automated reordering based on predefined thresholds, and accurate demand forecasting. By aligning production with demand, manufacturers can reduce carrying costs, minimize stockouts, and optimize working capital.
Complex Order Fulfillment:
Electric fondue set manufacturers often face challenges in efficiently managing order fulfillment processes. Manual order processing can lead to errors, delays, and customer dissatisfaction. A customized ERP system automates order management, enabling seamless order tracking, accurate delivery scheduling, and real-time updates for customers. With enhanced visibility into the order fulfillment process, manufacturers can improve customer satisfaction, reduce order lead times, and enhance overall operational efficiency.
Supplier Management and Procurement:
Establishing and maintaining effective relationships with suppliers is crucial for electric fondue set manufacturers. However, without a centralized system, managing supplier information, monitoring performance, and ensuring timely procurement can become a daunting task. A customized ERP solution integrates supplier management, automates purchase orders, facilitates supplier communication, and enables real-time visibility into supplier performance. These features streamline procurement processes, reduce lead times, and enhance collaboration with suppliers, ultimately resulting in cost savings and improved product quality.
Inadequate Analytics and Forecasting:
Accurate demand forecasting and production planning are vital for electric fondue set manufacturers to optimize resources, minimize waste, and meet customer expectations. Traditional methods relying on manual calculations and historical data can be time-consuming and prone to errors. A customized ERP system provides powerful analytics capabilities, leveraging real-time data and advanced algorithms to generate accurate demand forecasts, production schedules, and resource requirements. Manufacturers can make data-driven decisions, identify trends, and respond quickly to changing market demands, leading to improved operational efficiency and increased profitability.
See How My Company Can Massively Automate Your Company Departments
Custom CRM Development – For Organizations to manage its Customer Interactions in addition to Sales, Marketing, Billing, Products, Services, Contacts, Customer Support, among other things.
Custom ERP Development – For Manufacturers to handle BOM, Quotation, Order, RFQ, PO, SOA, Manufacturing, Trading, Inventory, Quality Control, Logistics, Shipments, and so on.
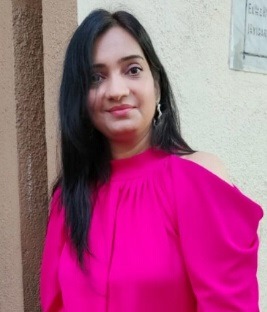
Conclusion
Electric fondue set manufacturers face a range of pain points in their operations, from inefficient production planning and inventory control to complex order fulfillment and inadequate analytics. A customized ERP solution tailored to the specific needs of the industry can significantly alleviate these challenges. By automating and integrating key functions, a customized ERP system empowers manufacturers to optimize production efficiency, streamline supplier management, improve inventory control, and enhance overall operational performance. Embracing a tailored ERP solution can enable electric fondue set manufacturers to deliver complete and stylish products while staying ahead in today’s competitive market.
Use Case: Streamlining Electric Fondue Set Manufacturing with Customized ERP
Company: FondueTech Manufacturing
Background: FondueTech Manufacturing is a leading provider of electric fondue sets, offering innovative designs and high-quality products. As the demand for their fondue sets continues to grow, the company faces operational challenges in effectively managing their manufacturing processes. To overcome these obstacles and stay ahead of the competition, FondueTech Manufacturing decides to implement a customized Enterprise Resource Planning (ERP) system tailored specifically for their electric fondue set manufacturing business.
Challenges Faced by FondueTech Manufacturing
Inefficient Production Planning:
FondueTech Manufacturing struggles with manual production planning processes, leading to delays, production bottlenecks, and inefficient resource allocation. The lack of real-time visibility into production schedules hinders their ability to meet customer demands promptly.
Inventory Control Issues:
Managing inventory levels poses a challenge for FondueTech Manufacturing. Inaccurate demand forecasting and manual inventory tracking often result in overstocking or understocking, leading to increased carrying costs or missed sales opportunities, respectively.
Complex Order Fulfillment:
FondueTech Manufacturing relies on manual order processing, which is prone to errors and delays. This affects their ability to provide accurate order tracking and timely delivery to customers, resulting in decreased customer satisfaction and potential revenue loss.
Supplier Management and Procurement:
The company struggles to maintain effective relationships with suppliers due to the absence of a centralized system for supplier management. This results in difficulties in tracking supplier performance, delays in procurement, and potential quality issues.
Inadequate Analytics and Forecasting:
FondueTech Manufacturing lacks comprehensive analytics and forecasting capabilities. Manual calculations and historical data analysis are time-consuming and offer limited insights, making it challenging to make informed decisions regarding production planning, resource allocation, and demand forecasting.
How a Customized ERP Solution Addresses the Challenges
Streamlined Production Planning:
The customized ERP solution integrates FondueTech Manufacturing’s production processes, automating workflows, and providing real-time visibility into production schedules. Production planning becomes efficient with automated notifications, optimized resource allocation, and streamlined communication among departments, resulting in improved productivity and reduced lead times.
Enhanced Inventory Control:
The ERP system enables real-time inventory tracking, automated reorder points, and demand forecasting based on historical data and market trends. FondueTech Manufacturing gains better visibility into stock levels, ensuring optimal inventory management, reduced carrying costs, minimized stockouts, and improved order fulfillment.
Simplified Order Fulfillment:
The ERP solution automates order management processes, including order tracking, scheduling, and invoicing. Customers receive real-time updates on their orders, improving transparency and customer satisfaction. FondueTech Manufacturing can fulfill orders accurately and efficiently, reducing errors, minimizing lead times, and enhancing the overall customer experience.
Streamlined Supplier Management and Procurement:
The ERP system centralizes supplier information, allowing FondueTech Manufacturing to evaluate supplier performance, track delivery timelines, and maintain effective communication. Automated purchase orders and streamlined procurement processes ensure timely delivery of raw materials, minimizing production delays and quality issues.
Advanced Analytics and Forecasting:
The customized ERP solution uses advanced analytics and real-time data. It generates accurate demand forecasts, production schedules, and resource requirements. FondueTech Manufacturing gains insights into market trends. This enables them to adjust production levels proactively, optimize resource allocation, and meet changing customer demands effectively.
Conclusion
By implementing a customized ERP solution, FondueTech Manufacturing can overcome the challenges faced in their electric fondue set manufacturing business.
The streamlined production planning and improved inventory control enhance operations. Simplified order fulfillment and supplier management improve efficiency. Advanced analytics optimize performance. These features help reduce costs and boost customer satisfaction, keeping the company competitive.
FondueTech Manufacturing can streamline processes with a tailored ERP system. This allows them to deliver stylish electric fondue sets efficiently. They are setting new benchmarks in the industry.