ERP for Electric Cookie Press Manufacturers: Enhance Operations
The electric cookie press manufacturing industry is rapidly growing, fueled by the increasing demand for convenient baking appliances. However, as this sector expands, manufacturers often face numerous challenges that hinder their ability to streamline operations and maximize efficiency. Inefficient production planning, inadequate inventory control, cumbersome order processing, and limited supply chain management capabilities are just a few of the pain points experienced by electric cookie press manufacturers. Fortunately, a customized Enterprise Resource Planning (ERP) solution tailored specifically for this industry can alleviate these challenges and empower businesses to thrive in the competitive market.
Pain Points
Inefficient Production Planning:
Manufacturers often struggle with optimizing their production processes due to a lack of real-time data, manual planning methods, and difficulty in tracking production progress. This can result in under or overproduction, leading to increased costs and customer dissatisfaction. A customized ERP for electric cookie press manufacturing enables manufacturers to create accurate production plans based on real-time data, ensuring efficient resource allocation, scheduling, and monitoring. With better visibility into the production process, manufacturers can meet customer demands promptly and reduce operational inefficiencies.
Inadequate Inventory Control:
Maintaining optimal inventory levels is critical for electric cookie press manufacturers. Excessive inventory ties up valuable capital, while inadequate stock leads to missed sales opportunities and dissatisfied customers. A customized ERP solution provides manufacturers with a comprehensive view of inventory levels, allowing for accurate demand forecasting, automatic replenishment, and efficient inventory management. Real-time inventory tracking ensures that production aligns with demand, reducing carrying costs and minimizing stockouts.
Cumbersome Order Processing:
Manual order processing is time-consuming, error-prone, and lacks visibility. Electric cookie press manufacturers often struggle with managing customer orders, tracking order status, and communicating order updates. A customized ERP system streamlines the entire order processing cycle, from order placement to fulfillment and delivery. Automated order capture, order tracking, and integrated communication tools enable manufacturers to enhance customer service, reduce order errors, and provide timely updates to customers. This results in improved customer satisfaction and increased operational efficiency.
Limited Supply Chain Management:
Effective supply chain management is crucial for electric cookie press manufacturers to maintain a smooth flow of materials, coordinate with suppliers, and manage production timelines. Traditional manual processes can lead to delays, inconsistencies, and miscommunications across the supply chain. A customized ERP solution for electric cookie press manufacturing integrates supply chain management functionalities, enabling seamless collaboration with vendors, real-time inventory visibility, and optimized procurement processes. By automating supplier interactions, manufacturers can minimize lead times, reduce costs, and ensure the timely delivery of raw materials.
Lack of Sales Trend Analytics:
Understanding market trends and customer preferences is essential for electric cookie press manufacturers to make informed business decisions. Without access to accurate sales data and analytics, manufacturers may struggle to identify emerging trends, forecast demand, and optimize product offerings. A customized ERP solution equips manufacturers with advanced analytics capabilities, enabling them to track sales trends, analyze customer behavior, and gain insights into product performance. By leveraging these analytics, manufacturers can align their production and marketing strategies to meet evolving customer needs and stay ahead of the competition.
See How My Company Can Massively Automate Your Company Departments
Custom CRM Development – For Organizations to manage its Customer Interactions in addition to Sales, Marketing, Billing, Products, Services, Contacts, Customer Support, among other things.
Custom ERP Development – For Manufacturers to handle BOM, Quotation, Order, RFQ, PO, SOA, Manufacturing, Trading, Inventory, Quality Control, Logistics, Shipments, and so on.
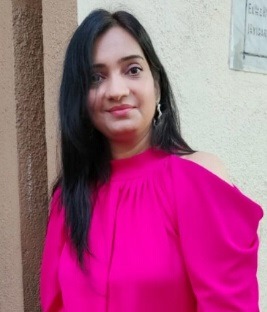
Conclusion
The electric cookie press manufacturing industry faces several challenges that impede business growth and efficiency. Adopting a customized ERP solution tailored for this industry helps manufacturers overcome these pain points and unlock their potential. Streamlined production planning, enhanced inventory control, and efficient order processing are enabled. Supply chain management is optimized, and insightful analytics are provided. Manufacturers deliver precise and efficient electric cookie presses while meeting customer demands effectively through ERP. Leveraging ERP helps electric cookie press manufacturers stay competitive, improve operational performance, and drive sustainable growth in the dynamic market.
Use Case: Optimizing Production and Inventory Management for an Electric Cookie Press Manufacturer
Company Background:
ABC Appliances is a leading electric cookie press manufacturer that prides itself on delivering high-quality baking appliances to customers worldwide. As their business continues to grow, ABC Appliances faces challenges in effectively managing production and inventory, leading to inefficiencies and missed sales opportunities. To address these pain points, they decide to implement a customized ERP solution designed specifically for the electric cookie press manufacturing industry.
Challenges Faced by ABC Appliances
Inefficient Production Planning:
ABC Appliances struggles with manual production planning processes, resulting in bottlenecks, resource wastage, and delays in meeting customer demands. They lack real-time visibility into production progress, making it difficult to adjust schedules or allocate resources effectively.
Inadequate Inventory Control:
ABC Appliances faces challenges in maintaining optimal inventory levels. Excessive stock ties up capital, while insufficient inventory leads to missed sales opportunities and dissatisfied customers. They lack accurate demand forecasting and struggle with manual inventory tracking and replenishment processes.
Cumbersome Order Processing:
The manual order processing system at ABC Appliances causes delays, errors, and communication gaps. They find it challenging to track order status, respond to customer inquiries promptly, and provide accurate delivery estimates.
Limited Supply Chain Management:
ABC Appliances experiences difficulties in coordinating with suppliers, managing procurement timelines, and ensuring timely delivery of raw materials. Manual processes and communication limitations result in delays and inefficiencies across the supply chain.
Solution
Implementing a Customized ERP System ABC Appliances decides to implement a tailored ERP solution to address their pain points and streamline their operations. The ERP system provides the following key features and benefits:
Streamlined Production Planning:
The ERP system enables ABC Appliances to create accurate production plans based on real-time data. They can monitor resource availability, track production progress, and adjust schedules as needed. With improved visibility into the production process, they can efficiently allocate resources, optimize workflow, and ensure timely delivery of electric cookie presses.
Efficient Inventory Management:
The ERP solution provides ABC Appliances with real-time inventory tracking, demand forecasting, and automatic replenishment capabilities. With accurate inventory data, they can avoid stockouts or excess inventory. The system generates alerts for low stock levels, allowing proactive procurement and ensuring that production aligns with demand. This reduces carrying costs, minimizes stockouts, and improves overall inventory management.
Streamlined Order Processing:
The ERP system automates the entire order processing cycle, from order capture to fulfillment and delivery. ABC Appliances can efficiently process orders, track order status, and provide customers with real-time updates. Automated workflows and communication tools enhance customer service and reduce errors, leading to improved customer satisfaction.
Optimized Supply Chain Management:
With the ERP system, ABC Appliances can seamlessly collaborate with suppliers, streamline procurement processes, and monitor supplier performance. Real-time visibility into the supply chain enables them to manage procurement timelines effectively, minimize lead times, and ensure timely delivery of raw materials. This enhances overall supply chain efficiency and reduces costs.
Conclusion
By implementing a customized ERP solution, ABC Appliances addresses their pain points and optimizes their electric cookie press manufacturing. They streamline production planning, control inventory efficiently, automate order processing, and optimize supply chain management. This improves operational efficiency and meets customer demands effectively, driving business growth. The ERP system empowers ABC Appliances to deliver precise and efficient electric cookie presses, maintaining a competitive edge in the market.