ERP for Electric Bag Sealer Manufacturers: Boost Operations
In today’s competitive business landscape, manufacturers of electric bag sealers face numerous challenges in effectively managing their operations. From inventory management to production planning and order fulfillment, these businesses must find efficient solutions to streamline their processes and enhance productivity. This is where a customized ERP for Electric Bag Sealer Manufacturers can make a significant difference. By addressing the pain points faced by manufacturers, a well-designed ERP solution can revolutionize the way these businesses operate, enabling them to deliver reliable and efficient products consistently.
Pain Points
Inventory Management:
One of the primary pain points in electric bag sealer manufacturing is effectively managing inventory. Without proper visibility and control over inventory levels, manufacturers can face overstocking or stockouts, leading to financial losses and customer dissatisfaction. A customized ERP system can integrate inventory management modules, providing real-time updates on stock levels, tracking product movement, and automating reorder processes. By optimizing inventory levels and reducing excess stock, manufacturers can minimize carrying costs and maximize profitability.
Production Planning:
Efficient production planning is crucial for electric bag sealer manufacturers to meet customer demands while maintaining cost-effectiveness. However, without proper coordination between departments and accurate forecasting, production inefficiencies and delays can occur. A customized ERP solution can centralize production planning, enabling manufacturers to align production schedules with sales forecasts, monitor work orders, and allocate resources effectively. By automating and streamlining production planning processes, manufacturers can minimize downtime, improve resource utilization, and ensure timely delivery of electric bag sealers.
Order Fulfillment:
Timely order fulfillment is vital for customer satisfaction and retention. However, without a well-integrated system, manufacturers may struggle to process orders efficiently, leading to delayed deliveries and dissatisfied customers. A customized ERP for electric bag sealer manufacturing can streamline the entire order fulfillment process, from order entry to shipment tracking. By integrating sales, inventory, and logistics modules, manufacturers can automate order processing, generate accurate invoices, and provide real-time order status updates to customers. This seamless workflow enhances customer experience and builds trust in the brand.
Supplier Management and Procurement:
Reliable suppliers and efficient procurement processes are critical for maintaining the quality and consistency of electric bag sealers. However, manual supplier management and procurement methods can be time-consuming and error-prone. A customized ERP system can digitize and automate supplier management, enabling manufacturers to maintain a comprehensive supplier database, track performance metrics, and streamline procurement processes. By integrating procurement with inventory management, manufacturers can optimize purchase orders, reduce lead times, and ensure a steady supply of raw materials, ultimately enhancing product quality and reliability.
Analytics and Forecasting:
Accurate demand forecasting and data-driven decision-making are essential for electric bag sealer manufacturers to optimize production, inventory, and resource allocation. Traditional methods of data analysis and forecasting may be inefficient and prone to errors. A customized ERP solution can incorporate advanced analytics tools, leveraging historical data, market trends, and customer insights to provide accurate demand forecasts. By empowering manufacturers with actionable insights, they can make informed decisions, minimize inventory waste, and adapt quickly to market fluctuations.
See How My Company Can Massively Automate Your Company Departments
Custom CRM Development – For Organizations to manage its Customer Interactions in addition to Sales, Marketing, Billing, Products, Services, Contacts, Customer Support, among other things.
Custom ERP Development – For Manufacturers to handle BOM, Quotation, Order, RFQ, PO, SOA, Manufacturing, Trading, Inventory, Quality Control, Logistics, Shipments, and so on.
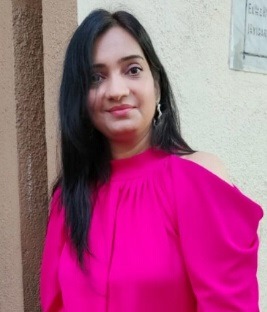
Conclusion
The challenges faced by electric bag sealer manufacturers can significantly impact their operational efficiency and customer satisfaction. However, by implementing a customized ERP solution specifically designed for this industry, manufacturers can overcome these pain points effectively. Streamlining inventory management, optimizing production planning, automating order fulfillment, and improving supplier management and procurement processes, a tailored ERP system revolutionizes operations, leading to enhanced productivity, cost savings, and consistently reliable electric bag sealers. Embracing technology and harnessing the power of ERP, manufacturers can thrive in a highly competitive market and meet the evolving needs of their customers.
Use Case: Streamlining Operations for Electric Bag Sealer Manufacturing with Customized ERP
Company Background:
ABC Manufacturing is a leading manufacturer of electric bag sealers, catering to a wide range of industries worldwide. With a strong focus on quality and innovation, the company has experienced rapid growth in recent years. However, as the business expanded, ABC Manufacturing faced several pain points in managing their operations efficiently. They realized the need for a comprehensive solution that could streamline their processes and enhance productivity. This led them to explore and implement a customized Enterprise Resource Planning (ERP) system specifically designed for electric bag sealer manufacturing.
Challenge
ABC Manufacturing encountered several challenges that were hindering their growth and affecting customer satisfaction. Their pain points included:
Disconnected Systems:
The company relied on multiple standalone systems and manual processes, leading to data silos, duplication of efforts, and limited visibility across departments. This lack of integration resulted in inefficiencies and delays in decision-making.
Inefficient Inventory Management:
The company struggled to maintain optimal inventory levels due to inaccurate demand forecasting and manual tracking. This resulted in stockouts and overstocking, impacting production schedules and financial performance.
Fragmented Production Planning:
With manual production planning processes, ABC Manufacturing faced difficulties in coordinating production schedules, resource allocation, and timely order fulfillment. Lack of visibility into real-time data led to missed deadlines and production bottlenecks.
Manual Order Processing:
Order entry, invoicing, and shipment tracking were time-consuming and prone to errors. This resulted in delayed deliveries, dissatisfied customers, and increased administrative burden.
Procurement Inefficiencies:
The company faced challenges in managing suppliers, tracking performance, and ensuring timely procurement of raw materials. Manual procurement processes led to delays, quality issues, and increased costs.
Solution
Customized ERP Implementation Recognizing the need for a comprehensive solution, ABC Manufacturing partnered with an ERP vendor specializing in home appliance manufacturing. The ERP solution was customized to address their specific pain points and streamline their operations.
Integrated System:
The ERP system seamlessly integrated all departments, enabling real-time data sharing and collaboration. This eliminated data silos and improved cross-functional communication, leading to streamlined processes and faster decision-making.
Enhanced Inventory Management:
The ERP system incorporated robust inventory management modules that provided accurate demand forecasting, inventory tracking, and automated reorder processes. This helped ABC Manufacturing optimize inventory levels, reduce carrying costs, and minimize stockouts and overstocking.
Streamlined Production Planning:
The ERP system centralized production planning, allowing ABC Manufacturing to align production schedules with sales forecasts, optimize resource allocation, and track work orders. Real-time data visibility empowered the company to eliminate production bottlenecks, reduce downtime, and improve on-time delivery.
Automated Order Processing:
The ERP system automated the entire order processing cycle, from order entry to shipment tracking. Integrated sales, inventory, and logistics modules streamlined the process, reducing manual errors, improving order accuracy, and providing real-time order status updates to customers.
Efficient Procurement:
The ERP system digitized supplier management, maintaining a comprehensive supplier database and enabling performance tracking. Integration with inventory management facilitated optimized purchase orders, reduced lead times, and ensured a steady supply of raw materials.
Results
By implementing the customized ERP solution, ABC Manufacturing achieved significant improvements in their operations:
Improved Efficiency:
The integrated ERP system eliminated manual processes, reduced redundancies, and improved overall operational efficiency. Employees had access to real-time data, enabling them to make informed decisions quickly.
Enhanced Customer Satisfaction:
With streamlined order processing and improved production planning, ABC Manufacturing experienced reduced order fulfillment time and fewer errors. This resulted in higher customer satisfaction, repeat business, and improved brand reputation.
Optimal Inventory Management:
Accurate demand forecasting and automated inventory tracking enabled ABC Manufacturing to maintain optimal inventory levels, reducing stockouts and overstocking. This led to cost savings and improved cash flow.
Streamlined Production:
Centralized production planning and real-time data visibility helped ABC Manufacturing eliminate bottlenecks, optimize resource utilization, and improve on-time delivery. This resulted in increased productivity and customer trust.
Efficient Procurement:
The digitized supplier management and streamlined procurement processes enabled ABC Manufacturing to maintain strong relationships with suppliers, reduce lead times, and ensure a consistent supply of high-quality raw materials.
Conclusion
The implementation of a customized ERP system transformed ABC Manufacturing’s operations, addressing their pain points and optimizing their processes. By integrating systems, enhancing inventory management, streamlining production planning, automating order processing, and improving procurement efficiency, the company achieved increased productivity, cost savings, and improved customer satisfaction. The ERP system provided ABC Manufacturing with the agility and insights necessary to navigate the challenges of electric bag sealer manufacturing and thrive in a competitive market.