ERP for Air Cooler Manufacturers: Streamline Overall Operations
The air cooler manufacturing industry has witnessed significant growth in recent years due to the increasing demand for energy-efficient cooling solutions. However, as the industry expands, so do the challenges faced by air cooler manufacturers. Inefficient inventory management, production planning issues, and disjointed supply chain processes can hinder growth and profitability. To address these pain points and enhance operational efficiency, customized Enterprise Resource Planning (ERP) solutions tailored specifically for air cooler manufacturers have emerged as a game-changer.
Pain Points
Streamlining Inventory Management:
One of the most pressing pain points for air cooler manufacturers is inefficient inventory management. Traditional systems often rely on manual processes, leading to errors, inaccuracies, and delays. This can result in excess stock, shortages, and increased carrying costs. A customized ERP system can resolve these issues by automating inventory tracking and management, allowing real-time visibility into stock levels, procurement needs, and demand patterns. By integrating data from various departments, such as production, sales, and procurement, the ERP system optimizes inventory levels, reduces carrying costs, and ensures timely replenishment.
Enhancing Production Planning:
Effective production planning is crucial for air cooler manufacturers to meet customer demands while minimizing costs. However, manual planning processes and disconnected systems can lead to production inefficiencies, increased lead times, and delays. A customized ERP solution provides a centralized platform where manufacturers can streamline and automate production planning. By integrating sales forecasts, inventory data, and production capabilities, the ERP system enables accurate demand forecasting and efficient production scheduling. This, in turn, reduces lead times, improves on-time delivery, and enhances overall customer satisfaction.
Simplifying Supplier Management and Procurement:
Air cooler manufacturers rely on a vast network of suppliers to source components and raw materials. However, managing multiple suppliers, negotiating contracts, and ensuring timely deliveries can be complex and time-consuming. A customized ERP system simplifies supplier management and procurement processes by providing a single platform for supplier collaboration, order management, and performance tracking. Manufacturers can leverage the ERP’s features, such as automated purchase order generation, supplier evaluation metrics, and real-time communication channels, to streamline procurement, reduce costs, and maintain strong supplier relationships.
Harnessing Analytics for Informed Decision-Making:
Data analytics plays a crucial role in identifying sales trends, predicting demand patterns, and optimizing inventory levels. However, many air cooler manufacturers struggle to extract meaningful insights from their data due to fragmented systems and lack of analytical tools. A customized ERP solution integrates advanced analytics capabilities, enabling manufacturers to analyze sales data, track market trends, and identify opportunities for improvement. With real-time dashboards and reports, manufacturers can make data-driven decisions, optimize product offerings, and respond swiftly to changing market dynamics.
Achieving Cost Efficiency:
Achieving cost efficiency is a primary concern for air cooler manufacturers as competition intensifies. Inefficient processes, wasted resources, and inadequate cost control can erode profitability. A customized ERP system helps address these concerns by optimizing resource allocation, automating repetitive tasks, and reducing manual errors. With improved inventory management, streamlined production planning, and better procurement processes, manufacturers can reduce costs, eliminate waste, and improve overall operational efficiency.
See How My Company Can Massively Automate Your Company Departments
Custom CRM Development – For Organizations to manage its Customer Interactions in addition to Sales, Marketing, Billing, Products, Services, Contacts, Customer Support, among other things.
Custom ERP Development – For Manufacturers to handle BOM, Quotation, Order, RFQ, PO, SOA, Manufacturing, Trading, Inventory, Quality Control, Logistics, Shipments, and so on.
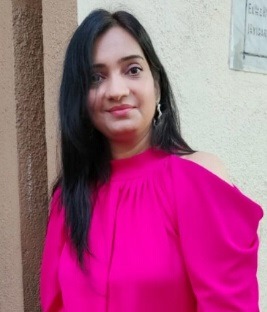
Conclusion
In the highly competitive air cooler manufacturing industry, staying ahead requires embracing technology that can address critical pain points. A customized ERP solution tailored specifically for air cooler manufacturers provides a comprehensive platform to streamline inventory management, enhance production planning, simplify supplier management and procurement, harness analytics for informed decision-making, and achieve cost efficiency. By implementing such a solution, air cooler manufacturers can optimize their business operations, deliver efficient and cost-effective air coolers, and gain a competitive edge in the market.
Use Case: Streamlining Production Planning for Air Cooler Manufacturing
Challenge
ABC Air Coolers is a well-established air cooler manufacturing company that produces a wide range of energy-efficient cooling solutions. Despite their success, they face challenges in efficiently managing their production planning process. The manual approach to production planning leads to inaccuracies, delays, and increased costs. ABC Air Coolers recognizes the need for a customized ERP solution to streamline their production planning and enhance operational efficiency.
Customized ERP for Production Planning
Automated Demand Forecasting:
The customized ERP system integrates historical sales data, market trends, and customer demand patterns to provide accurate demand forecasts. By leveraging advanced algorithms and statistical models, ABC Air Coolers can generate reliable sales forecasts for different product models and geographical regions. This allows them to plan their production schedules more effectively and allocate resources accordingly.
Real-Time Inventory Management:
The ERP system provides real-time visibility into inventory levels, including raw materials, components, and finished goods. ABC Air Coolers can monitor stock levels, track material requirements, and identify potential shortages or excess inventory. This information enables them to optimize inventory levels, reduce carrying costs, and avoid production bottlenecks caused by insufficient materials.
Efficient Production Scheduling:
With the customized ERP solution, ABC Air Coolers can automate the production scheduling process. By considering factors such as demand forecasts, available resources, and machine capacities, the ERP system generates optimized production schedules. This ensures that production lines operate at their maximum efficiency, minimizing idle time and reducing lead times. The system also considers production constraints, such as machine maintenance or labor availability, to avoid disruptions and optimize overall productivity.
Collaborative Workflows:
The ERP system facilitates collaboration among various departments involved in the production planning process. Production managers, procurement teams, and sales representatives can access a shared platform to communicate and exchange information. This ensures that everyone is aligned with the production schedule, enabling effective coordination and avoiding miscommunication or delays. The system also allows stakeholders to track the progress of each production order in real time, ensuring transparency and accountability.
Exception Handling and Alerts:
The ERP system is equipped with exception handling mechanisms and automated alerts. If there are any deviations from the planned production schedule or inventory levels fall below a certain threshold, the system triggers alerts to notify the relevant personnel. This proactive approach enables ABC Air Coolers to address issues promptly, make necessary adjustments, and avoid potential disruptions to their production processes.
Benefits
By implementing the customized ERP solution for production planning, ABC Air Coolers can experience several benefits:
Improved Accuracy:
The ERP system eliminates manual errors and improves accuracy in demand forecasting, resulting in better production planning and resource allocation.
Reduced Lead Times:
Streamlined production scheduling and real-time visibility into inventory levels minimize delays, enabling ABC Air Coolers to meet customer demands faster and enhance customer satisfaction.
Cost Optimization:
The optimized production planning and inventory management capabilities of the ERP system help ABC Air Coolers reduce carrying costs, minimize wastage, and maximize resource utilization.
Enhanced Collaboration:
The collaborative workflows and shared platform facilitate effective communication and coordination between departments, leading to smoother production processes and improved interdepartmental collaboration.
Agile Decision-Making:
With real-time data and analytics provided by the ERP system, ABC Air Coolers can make informed decisions, adapt quickly to market changes, and optimize their production strategies for maximum efficiency and profitability.
In conclusion, the customized ERP solution for production planning empowers ABC Air Coolers to overcome the challenges associated with manual production planning processes. By leveraging automation, real-time data, and collaborative workflows, they can streamline their production planning, optimize resources, reduce costs, and deliver high-quality air coolers efficiently to meet customer demands.